Making a bar stool with your own hands
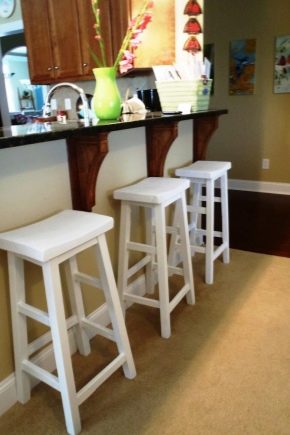
Bar stools have become an indispensable attribute of the arrangement of kitchen space.
Now in a fashion apartment in the style of a loft, where the kitchen is combined with the living quarters, all the extra partitions are dismantled. Bar counters are the "border", denoting a living area, and a place for eating in the kitchen. Not surprisingly, such attributes have become a sought-after piece of furniture.
People who like to make with their own hands can make such a simple object on their own, especially since it's technically easy to implement.
What tools are needed?
Here you need a standard set of tools, materials and a correctly drawn drawing.This homemade chair is a product with high legs about 80 cm high, below there is a special footrest. High coasters are very comfortable, in the process of sitting legs do not numb and do not get tired.
Height may vary depending on the size of the bar in the kitchen. A person should feel free and not be afraid of losing the center of gravity, despite the fact that the chair is above standard sizes.
Making a model of plywood
Wood - plastic material, easy to process. You will need tools:
- Bulgarian with disc type - "saw";
- Sanding machine;
- Roulette;
- Drill and screws;
- Glue.
- Chisel;
- Screwdriver.
Performance of work
At the very beginning of work, elements of the future wooden legs are cut out of wood. The marking in the form of the letter A is applied on the tree, decorative roundings are made at the intersection points.
The elements of the legs are cut out with a jigsaw on lined markings. Thus, the block turns out - future support for legs. This is an important connecting element: there will be few fastenings, therefore the support for the legs is reliably bound to fasten the supports that must withstand decent loads.
The chair must be durable and not "hang out" at the points of attachment of nodes. All places of cuts are processed by the grinding machine.
After the details of the legs are made, it's time to assemble the supports. Four blocks of legs are carefully coated with glue and mounted close to each other in the lining. After the glue hardens, for greater strength, self-tapping screws should be wrapped around the fastening points.
Footrest cut out of plywood. If the thickness of the material is insufficient, then the cut pieces of plywood can be glued and joined.
The seat is made on the same technology. The cut pieces that are well pre-glued are connected. You can make several layers of plywood, taking into account the possible large loads.
A special substrate is made under the seat, it must be strong enough, because the legs will be attached to it.
Fastening occurs with the help of screws. When everything is dry and will be collected, there will come a stage of paint and varnish.
Solid product
The best option is to make a solid bar stool:
- Birch;
- Oak;
- Pine.
The birch massif is preferable, the pine is not always uniformly painted over.
In the manufacture of a chair from a solid array, you need to take into account - the thickness of the material must be at least two centimeters.
A circle with a diameter of 370 mm is cut out - this will be the future seat. If there is no special woodworking equipment in the house, then the profile is outlined along the contour, cut out, the surface is machined with a grinder.
Then a circle smaller than 250 mm is made - this is the part that will be the footrest. All elements are also cut from wood, with wood fibers must go along.
Then they are connected with glue, the back is fixed with screws. It is enough such fastening that the design was rigid and strong. After polishing, you should carefully paint over the resulting object, cover with several layers of varnish.
A chair made of solid wood is heavier, but also more durable. It is easy to stylize antique, then it will look very original. In this style, you can make more than one product. Such a thing will serve for a long time, it is not afraid of changes in either humidity or temperature.
The technological flaws of the tree
Wooden furniture is in constant demand, but it also has its drawbacks:
- Susceptibility to moisture is the most dangerous factor that damages wood;
- The anisotropic structure affects the different characteristics of wood fibers located up and down;
- Timber is combustible and prone to fungal diseases.
If wooden objects are present for a long time in the fresh air, for example, on the veranda of a private household, then it is likely that they will deteriorate, especially with products in which plywood is present.
Making of metal, the first option
Metal is durable, and products from it are no less elegant than from wood. To make bar stools from metal does not represent the big complexity. We need appropriate materials and basic skills in welding.
Preparation for work is that appropriate tools are selected first. First of all, you need a pipe bender, you can create it yourself. On the layout should fix the bars and between them to leave a space equal to the diameter of the pipe. Two beams must be at least 5 cm thick.
The pipes are filled with sand, inserted between the bars, and then the operation begins to give them the desired shape.
Required tools
You will need:
- Drill and drill bits;
- Bushings;
- Screws with nuts and bolts;
- Self-tapping screws;
- Facing;
- Measuring tools and pencil;
- Paint and primer.
Start of creation
Before you begin to work, you should draw diagrams to first imagine what the object will be on high legs. Samples can be found on the Internet, where there is a huge variety of models; in the same place it is easy to find a description, and even diagrams and drawings. After the model is selected, it becomes clear what will be the dimensions the creation of a product in three-dimensional space begins:
- First of all, a stencil is made on a 1: 1 scale; it will become a benchmark for future manufactured blanks;
- Two pieces of a profile pipe up to two meters long are cut off (this will be the future frame);
- The crossbar will also be from the pipe, so you will need segments in the amount of two pieces with a length of 0.5 meters;
- The rear legs will also be 0.53 m;
- All material is cleaned with sandpaper;
- Pipes are bent according to the given pattern.
Installation of parts
Holes are drilled at the attachment points. Then the parts are assembled together, and iron cylinders are inserted into the holes. After that, a fabric blank is taken, and two pieces are cut out of it according to the pattern, which will be the seat and the backrest.
They are stitched with double stitching and dress on the finished frame. The screws are attached behind the legs.
For fasteners, you can use screws 5x80 mm in size for the legs. The seat is screwed to a small circle using self-tapping screws 5x40 mm. Installation of stiffeners can be done with 5x20 mm self-tapping screws.
The ribs are mounted on the legs using the corners. Thing is ready.
Increasingly, metal stools, back and armrests which may have solid iron or copper tubes.
If there is a bar in the house, then the chairs to it will be very appropriate. Handmade products can last a very long time, they are not afraid of either high humidity or large mechanical overloads.
Second option
If you have an idea to create chairs yourself, then it is recommended to analyze several algorithms for the manufacture of these simple items.The second option may be preferable especially for those who know how to use a welding machine.
To get started you should prepare a tool:
- Reiki width about 20 cm;
- Metallic profile;
- Scissors;
- Welding machine;
- Sander;
- Sandpaper;
- Ruler;
- Square;
- Marker;
- Roulette.
In a short time, it is easy to create an original product that can “work” for many years.
Installation
Stencils are made in compliance with the intended size. Slats are cut off - these will all be blanks for the seats. The strips are welded, the desired shape will appear as a result. The slats are cut into even smaller strips, they should fit inside.
Plywood is made stencil, which will serve as a guide. Thin strips are welded so that the shape appears.
It is necessary to grind the workpiece, round the corners. For the manufacture of the legs, a section profile of 3 cm is used. A detail of the required size is cut from it. The height of the model can be different, depending on the height of the bar. Usually the seat is 35 cm below the table top.
Made parts are welded to the frame, then the design will be sustainable.When everything is set correctly and checked several times, then you can “grab” by welding. The footrest is usually located forty centimeters from the seat, cross-pieces are cut and welded. Joints are polished.
Finish
Metal - hard material, be sure the ends of the legs are insulated with rubber or wooden nozzles. After the product is manufactured, the finishing period begins: the finished thing is primed and painted.
It makes sense to put several layers of soil and paint, which will guarantee a long successful operation of things.
How to make bar stools with your own hands, see the next video.