Solvents: features of choice and application
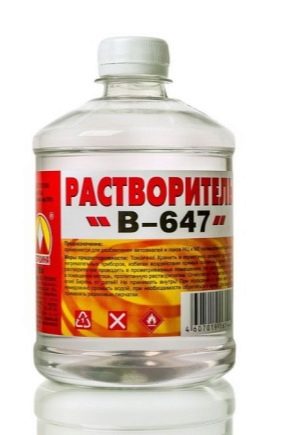
In the Russian market of paints and varnishes (LKM) today there is simply a huge amount of solvents, which differ in price, chemical composition, and application. This is due to the fact that a separate type of solvent, by applicability, corresponds exclusively to a specific type of paintwork material. Therefore, it is precisely the careful and accurate choice of solvent that is able to ensure the effectiveness and correctness of the technology for its application.
What it is?
The solvent in its classical definition is a liquid, solid or gaseous substance, which is capable of dissolving other solid, liquid or gaseous substances. The most famous inorganic solvent is ordinary water, which dissolves perfectly the various consistencies of inorganic and organic origin.
The spectrum of inorganic solvents (reagents) is safer in operation and is realized at budget prices. However, by their qualities, these compositions are not very compatible with the wide range of compositions to be dissolved. It is also important that this product has an extremely low level of volatility.
Organic is more effective, because these solvents have better functional characteristics. Such compositions are homogeneous and heterogeneous (combined). The first is mainly alcohol products.
Heterogeneous solvents (white spirit, turpentine and others) contain refined petroleum products and essential substances. In combination with a high degree of volatility, they have a pronounced flammability and toxicity, which requires following their strictest security measures. To evaluate the suitability of the use of a particular solvent in each case is necessary for its properties, such as density, appearance, volatility, water content and other qualities.
The characteristics of this reagent, as well as the technological features of working with it, are determined by a number of technical features, the main of which include:
- ethyl ether volatility;
- chemical purity;
- coagulation number;
- acid number;
- the proportion of water according to Fisher.
The degree of volatility of the composition shows the rate at which the diluted substances evaporate and correlates with the rate of evaporation of ethyl ether. From this indicator depends on the duration of drying paint. If the index is 6 units, this means that the composition evaporates 6 times slower than the reference ether.
In accordance with this, three groups of solvents are distinguished by volatility:
- easy flying - up to 7 units;
- mid-volatile - 7-13 units;
- low-volatility - more than 13 units.
From the volatility of the solvent depends not only the duration of drying paint, but also the method of its application, as well as the operational properties of the coating.
The volatility of the solvent affects the adhesion of the paint - there is a decrease in its level.
An important role in the process of selecting a solvent is played by the degree of its purity. The indicator reflects the quantitative content of various impurities contained in it. The higher the purity, the more efficient the solvent.. Accordingly, the level of purity increases and its value.There are 5 levels of cleanliness and each has its own label. For example, Level 1 - technical reagents ("T"), allow for the content of impurities up to 5%, other levels are reduced.
Particularly pure (“OFS” reagents) are usually referred to as reference. They are used in highly specialized areas (for example, in medicine). Technical analogues are used in construction and in everyday life.whose efficiency and price parameters meet the necessary requirements.
The number of coagulations is the indicator of the largest ratio of the volume of the reagent to the volume of the dissolved coatings with the nitrocellulose component. For example, the solvent has an indicator of 36%, that is, in the process of dilution in a ratio exceeding 37%, the nitrocellulose component will begin to precipitate, and the paint and varnish materials will lose their physical and chemical properties. In other words, the coagulation index is the allowable limit for mixing two reagents.
Acid number (CN) reflects the volume of special additives (usually potassium hydroxide), which neutralize the free acids in the paintwork material. The lower this parameter, the less reagent volume will be required to give the LKM optimal conditions.. The indicator is expressed in milligrams per 1 gram of the substance to be diluted (mg / g). For example, the “CN” of a product, 0.06 mg, means that in order to impart the desired state, paint and varnish materials should be no less than 6% of its entire volume. The use of smaller proportions will be unproductive.
Mass fraction of water according to Fisher is also an important indicator. The volume of water in the reagent should be standard and for each product have different values. Non-standard values of the index worsen the quality of the composition, reduce the level of its purity and volatility.
Purpose
Solvents as substances that change the properties of paintwork materials are used to improve their fluidity and viscosity. The main purpose of their application is to increase the efficiency of work.
And in this sense, they solve the following tasks:
- dilution of thick coatings to improve their fluidity and accelerate the working cycle;
- cleaning of various surfaces;
- cleaning, disinfecting and degreasing treated surfaces in order to improve adhesion;
- manufacture of adhesives;
- fabrication of impregnating consistencies that improve adhesion;
- cleaning work clothes and equipment.
Organic solvents are widely used in the production of a wide range of coatings.
They are used in dry cleaners, in everyday life (turpentine, acetone) to remove residual glue and varnishes (methyl alcohol, acetone, ethyl acetate), as a component in compositions intended for washing operations in the perfume industry (ethanol), in chemical synthesis processes and how degreaser.
As a rule, the solvent itself and the consistency it dissolves is to a certain extent similar, that is, there is a polar principle.
Organic solvents in construction and finishing works are used to bring to the required degree of viscosity various primers, putty consistencies and varnishes. They are used for degreasing tools and surfaces of products.
Based on these functions, solvents must meet the necessary requirements:
- do not react with paint coatings and have a high level of evaporation;
- have non-hygroscopicity (do not change the necessary qualities inherent in them, reacting with water);
- mixing reagents should effortlessly lead to a homogeneous consistency;
- the solvent should affect the coatings only at the time of its application to the surface and subsequently evaporate.
Types and characteristics
Compared with inorganic reagents, organic ones are used an order of magnitude more often due to their wider functional properties. Organic reagents are homogeneous and heterogeneous in composition.
Homogeneous 95–100% consist of the main chemical component - the base. Sometimes to reduce the concentration of the reagents can be dissolved in other environments, for example, in water. The cost of solvents of this group, as a rule, is less than the combined ones, but they have a narrower range of applicability for interaction with different materials.
Heterogeneous (number) - the reagents obtained by the method of mixing, differ in composition and manufacturing technology. By their price and efficiency, they differ significantly from homogeneous counterparts.
Another classification forms the following types of organic reagents for coatings:
- hydrocarbon;
- alcohol;
- ethers.
the first group - hydrocarbon, are:
- petrol;
- White Spirit;
- solvent;
- turpentine;
- benzenes.
They are flammable and do not dissolve in water.
- Turpentine used in two versions: gum and pnevny. The first one is of better quality, with no color or slightly yellowing substance with a boiling point of up to 180 °.The second is somewhat darker and spreads a pungent smell. The structure is widely used in work of LKM. Well reacting with ethers, alcohols and chlorinated derivatives, dissolves LKM, accelerating their drying. It is used for the preparation of mastic compositions, as well as wet grinding.
- White Spirit - a product of petroleum distillation, is an intermediate product between gasoline and kerosene fractions. Colorless, volatile, with a boiling temperature of not more than 165 °. The ability to dissolve paintwork materials is slightly lower than that of turpentine. Used in the wet grinding process.
- Petrol - volatile product of oil distillation. Flammable, forms explosive mixtures. Due to the high degree of volatility in the decoration of furniture is used very rarely.
- Benzene - mobile volatile substance without color. In practice, 90% and 50% formulations are used. Toxic, flammable, may form explosive mixtures. Rosin, wax, rubber and other substances are perfectly soluble in it. Used in the manufacture of varnishes (lowers the thickness) and as a solvent reagent for nitrolak.
The following group of reagents for paintwork materials are alcohols, of which ethyl and butyl are most widely used:
- Ethanol - a liquid substance without color resulting from the distillation of the products of fermentation of sugars. In the paintwork area, a fortress of at least 90 ° is used (a small degree of strength leads to marriage). Able to react with certain resins, such as shellac. It is used as a diluent along with reagents for nitrolak.
- Butyl alcohol - an excellent reagent for nitrocellulose lacquers, gives the film a quality look, reduces the whitening of the coating.
- Methyl alcohol - liquid product without color, obtained during the distillation of wood. As a rule, includes the addition of acetone and esters. In pure form, referred to as methanol. Well dissolves certain types of resins and oils. In some industries, the use of the product is limited due to its toxicity.
- Ethylene glycol - viscous liquid without color and odor. Mix well with water. It has a low evaporation rate, which has a positive effect on film formation and coating condition - it takes on an excellent appearance and is easier to polish. The product is used in the manufacture of varnishes, based on resin.
The last group is represented by ethers - methyl, ethyl, butyl and others. Products are used mainly as reagents with nitrocellulose and in the manufacture of these mixtures in order to bring the compositions to the required viscosity.
- Methyl acetate - liquid, low-boiling, poisonous, flammable, highly volatile substance (flash T - 13-16 °).
- Ethyl acetate - slightly volatile liquid substance (boiling point - 78-82 °). Mixed in different proportions with alcohols, ethers, fats and oils. Excellent resin and wax reagent.
- Butyl acetate - yellowish liquid with non-intensive evaporation. It is used as a retarder for the rate of drying, capable of preventing the whitening of the varnish film.
- Amyl acetate - liquid with a low level of evaporation. Excellent reagent for nitrocellulose, oils and certain types of resins. The scope is similar to butylacetate. Often used in the restoration of furniture.
- Acetone - highly volatile liquid with a pungent odor, perfectly dissolving nitrocellulose. Reagent is fire hazardous. In various proportions it is easily mixed with alcohols, ether compounds and water.
In order to bring paintwork materials to the required condition, they often use mixed reagent compositions, which have a significant impact on the state of the entire coating. With the prevalence of low-boiling acetone, methyl / ethyl acetate in the compositions, the lacquer becomes cloudy due to rapid evaporation, and the use of only high-boiling solvents, such as butyl acetate or amyl acetate, on the contrary, reduces the drying rate of the coating.
Modern industry supplies ready-made forms that are already matched to the respective brands of paints and varnishes, for example, P-4, P-5, P-645, 646, 647, 648, 649, 64 and AMP.
Today, there are both universal solvents on the market, for example, the popular product 646, and highly specialized:
- Solvent 1120 produced by Rostex Super is ideal for anti-corrosion primer. In this case, the composition is applied quickly and easily, and the surface after drying becomes flat and smooth.
- Solvent 1032 has been developed for working with alkyd paints with a spray method, which is also suitable for effective cleaning of instruments.
Manufacturers
There is a wide variety of organic and inorganic reagents of various grades.
According to the rating data, the following foreign brands are in the top ten in terms of sales:
- PPG (US);
- AkzoNobel (Netherlands);
- Henkel (Germany);
- Sherwin-Williams (United States);
- Valspar (United States);
- Axalta (USA);
- Basf (Germany);
- Kansai (Japan);
- Sika (Switzerland);
- Hammerite (UK).
Of the domestic brands are known and in demand products of the company "Russian Paint" and "Empils", "Novbytkhim".
- JSC "Russian paints" - the leading enterprise of the domestic paint and varnish industry. The developer of high-tech paints and coatings, producing about 300 types of products for automobile plants, enterprises of the oil and construction industry, the aircraft industry and the railway. The advanced innovation policy allows the enterprise to compete in real terms with the products of both Russian and foreign firms.
- ZAO Empils Founded in 1992, the main production facilities and office are located in Rostov-on-Don. The company specializes in the production of decorative and industrial paintwork. The company has mastered the production of high-quality paintwork materials of the budget line.
- Particularly popular products from St. Petersburg Novbythim company, founded in 1994 by young talented scientists and chemists of St. Petersburg Technical University.Now, the company produces more than 60 items of goods of excellent quality at budget prices.
Tips for choosing
It should be remembered that each type of paintwork material requires a well-defined type of solvent. More precisely, there are specific types of reagents for grease, glue, oil, paint, correction fluid, gypsum, varnish, cement grout, primer, rosin, and other paintwork materials. Therefore, the correct selection of the product is a guarantee of high-quality coverage, since it ensures the homogeneity of the mixture, the absence of disintegration, easy and fast work with it. Knowledge of the technical characteristics of the product helps in its selection.
The specificity of the solvent consists in the ability of rapid evaporation from the diluted substance, which gives it the required quality. Individual solutions have the quality of a siccative effect, reducing the drying time. The ability to accelerate the formation of a film in reagents is another function along with the main one (giving fluidity and reducing viscosity).
The volatility of the reagent directly affects the quality of the film formed by paint and varnish materials. To control the process, it is important to take into account that when the reagent of the coating is evaporated too quickly, they turn white, stains appear on them, the structure of the coating is deformed, its properties change.That is why in a number of cases the use of volatile solvents is not recommended.
About the likely level of volatility of the reagent can be judged by the boiling point. The smaller it is, the higher this property is, and vice versa. When choosing a product, you should especially focus on the external aspects of the reagent and compare them with the descriptions on the labels or in the product cards.
The main evaluation criteria are minor deviations in color, density, particles and precipitation. It is better not to buy such reagents.
Dissolving paintworking reagents are selected by manufacturers based on the speed and uniformity of the evaporation process. The cheap components they contain violate these processes.
For example, acetone in reagent 646 is too volatile, which prevents the optimum drying process of the film. Due to the extremely rapid evaporation, the formation of the surface film is too fast, which, in turn, prevents the release of residual volatile constituents from the deep layers. The result is “boiling”, loss of shine, low quality of the film. Negative effect on the film formation of acrylic paints and alcohols, abundantly available in domestic reagents. Water in alcohols disrupts the process of polymerization of these materials, leading to looseness of the resulting polymer film.
In order to clearly understand which specific reagent is suitable for a specific paintwork product, it is important to carefully study the description and the correspondence table.
When choosing and working with reagents, it is necessary to take into account such a feature of the product as the level of toxicity.
In this context, there are 3 indicators:
- The maximum allowable concentration in the work area (MPC) is an indicator reflecting the permissible degree of saturation with toxins.
- The coefficient of semi-lethal dose. For example, “LD50” means that when an organism receives a certain concentration of a product (mg), the probability of death is 50%.
- The average concentration of toxic evaporation emitted by the reagent until the final drying (determined according to a special table).
Safety
Often indicators of fire and explosion hazard of reagents are not noted in the descriptions. Therefore, they just need to know:
- Reagent flash point shows the minimum level at which it can release a volume of toxins sufficient to generate a steady fire.
- Reagent auto-ignition temperature - the lowest temperature level, where fumes can ignite without the participation of a third-party source of ignition.
- Reagent flash point - the lowest temperature level, where fumes can ignite from a spark (for individual reagents this temperature may be less than zero degrees).
Organic reagents are characterized by a significant level of toxicity, detrimental to human health.
That is why the work with them is required to adhere to special rules:
- availability of effective ventilation (supply and exhaust and exchange) at the workplace;
- the use of a respirator and workwear;
- exclusion of fire or sparks in the room;
- storage of reagents in special basements or warehouses. On the shelves, they should be corked up. Direct sunlight cannot be allowed.
Almost all organic reagents are active, and some (for example, ketones, amines and others), with their high content in the room lead to acute poisoning, and others cause allergies, dermatitis and other complications.
See the following video for the difference between thinners and solvents.