Types and features of laying concrete floors
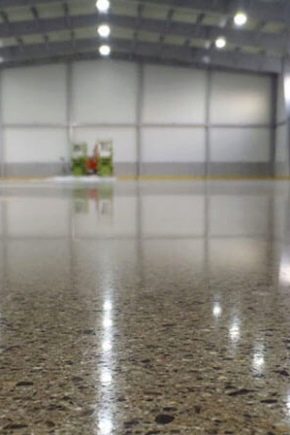
Concrete is a material that is often used to create floors. It must be laid on a special technology, but you can carry out the procedure yourself.
In order for the concrete paving to be laid correctly, it is necessary to get acquainted in advance not only with the steps of this process, but also with the features of the material itself. All these questions will be discussed in detail in this article.
Advantages and disadvantages
Floors, which are based on concrete, have special characteristics. Among them there are both positive and negative qualities.
The advantages of concrete coatings include the following parameters:
- Strength.Concrete is resistant to heavy loads and mechanical stress. The strength and strength of the structure depends on the density of the material. The higher its rate, the stronger will be the coating.
- There is no need to take care of such floors regularly.
- The material can serve as an excellent basis for laying a decorative coating.
- Concrete is not susceptible to various chemicals.
- The material is fireproof.
- Floors of this type are resistant to moisture.
- An important characteristic is the reasonable price for the material, which allows laying the floor even in large areas without any special financial costs.
Among the negative characteristics are the following:
- This type of raw material is not suitable for use as a finishing coating. For most people, the appearance of concrete is considered unaesthetic, so there is a need for additional finishing.
- The technology of mounting the material is very time consuming. The dismantling process is similar.
- Dust is actively accumulated on concrete surfaces, therefore it is necessary to carry out additional procedures to protect the material from dust accumulation.
- Concrete floors are not quite comfortable in terms of tactile sensations. This is another argument in favor of using concrete only as a rough base, because it is not always pleasant to walk on such a surface barefoot.
Device
In residential buildings, insulated concrete floors are often laid, the base of which is the ground.
In this case, the concrete structure has the following device:
- A gravel-sand mixture is applied to the recessed ground.
- The next layer is represented directly by the concrete base.
- Next, lay a layer of vapor barrier.
- After it is a thermostop, which is covered with a film of polyethylene.
- Top settles reinforced screed.
It is also important to familiarize yourself with the options for installing joints when laying a concrete floor.
There are three types of seams that prevent the formation of cracks on the surface:
- Constructional. They should be done if the floor was not filled at one time, especially if the interval between the fill areas exceeded 4 hours.
- If it is necessary to remove stress from the surface of the base, shrink-type seams are made.This technology is particularly relevant if it dries out unevenly after laying the floor due to environmental exposure.
- Insulating seams are very important when creating a concrete floor. These joints serve to prevent vibrations affecting the floor from affecting walls and other structures.
It is worth remembering that the creation of such coverage should be guided by a number of rules governing its device (SNiP).
For these floors, the following provisions of the SNiP should be taken into account:
- SNiP 31-06 It is the standard of conformity for technological maps of creating such floors in both residential and public buildings.
- SNiP 31-05 includes provisions relating to the creation of concrete floors in sports facilities and facilities.
- SNiP 10.03 regulates the technology of laying the floor in those buildings where animals will be kept. As a rule, slotted concrete floors are used for such structures, which help to make cleaning easier.
- If concrete floors are placed in a room where they will often be exposed to chemical attack, then it is necessary to focus on SNiP 2.03.11.
- SNiP 3.04.01 regulates the temperature that must be maintained indoors when laying concrete floors with special materials.
Polymer coatings can be laid if the temperature in the room is not lower than 15 degrees Celsius. When laying liquid glass, the temperature should not fall below +10, and bitumen mastics and cement mixtures can be used only with a thermometer reading not lower than +5 degrees.
If polyurethane floors are subsequently applied over the concrete base, the material must be thoroughly cleaned of dust and the upper layer, which is particularly fragile, must be removed.
Kinds
Concrete floors are available in various forms. At the heart of each classification of coatings lies a certain sign, significantly affecting the properties of the material.
The first criterion for the difference is the density of the raw material. The following concrete variations are distinguished:
- Ultralight porous concrete. Pumice is used as a filler in such material. The maximum density of such products is 500 kg / m³.
- Light coatings, the density of which does not exceed 1200 kg / m³, are based on three types of structure: porous with aggregates, coarse-grained and cellular.
- Lightweight coverings include such varieties whose density varies in the range from 1800 to 2200 kg / m³.
- Concrete materials that have a density of from 2,200 to 2,500 kg / m³ are considered heavy.
- When the density of the coating exceeds 2500 kg / m³, the material is considered particularly heavy.
Another parameter is the number of layers:
- Single-layer floors are most often made in small spaces. The maximum thickness of a layer of such a coating is 25 centimeters.
- Multi-layer floors involve the pouring of several concrete layers. Such a process is very labor intensive.
- The reinforced floors combine the increased durability and smaller thickness. A similar result is achieved through the use of materials such as steel mesh, fibers made of synthetic materials, rods and fibers made of steel.
A special kind of concrete floors is a self-leveling floor for industrial enterprises. Such materials usually cover large areas. This coating is made by a special technology, thanks to which the mixture is able to quickly harden.
Industrial self-leveling floors are modern type coatings that are used to create the front surface of floors.A feature of this material is its ability to self-level. This coating also forms a perfectly flat surface without joints and seams, and can also be painted by adding color pigments to its composition.
Such floors can be found in various public places - restaurants, cafes, cinemas. Their significant advantage is the ability to combine the function of both the main and decorative coatings.
Scope of application
Concrete floors are laid with the following objectives:
- alignment of the surface for finishing;
- to seal the flooring;
- implementation of raising the base level;
- creation of floor heating technology;
- often, when reconstructing various floors, multi-layer concrete floors are laid;
- Reinforced concrete coatings can often be seen in such rooms where a significant load is placed on the floors (such buildings include warehouses, machine parking lots, factory workshops).
Necessary tools and mixes
In order for the process of laying the concrete floor to be successful, you should take care in advance of the availability of all the necessary materials andtools. These include:
- vibrating plate;
- cement;
- sand;
- water;
- rubble;
- cord (twine);
- building level;
- buckets;
- jackhammer;
- trowel;
- concrete mixer;
- shovels;
- lighthouse rake;
- construction mop;
- the rule;
- half lter;
- formwork guides;
- adhesive tape;
- construction vacuum cleaner.
Also for the implementation of the work will need to purchase special compositions that affect the state of the concrete floor in the process of its laying and operation. These include:
- primer (necessary to carry out the drainage of the coating);
- hardener;
- plaster as an additional protection against moisture;
- glue for concrete (if you need to bond other concrete structures to the floor);
- reinforcing mesh;
- joint sealant;
- In order to remove dust from the finished surface, it is useful to use anti-dust treatment.
Only with all of the above elements, you can proceed directly to the laying of concrete pavement.
Preparatory work
An important step is the preparation of the base for concrete. It is carried out in several stages:
- The first step is to adjust the old base.Disassembly of damaged areas should be done very carefully. If the base has too many cracks and defects, it is easier to dismantle it and put in a new one. If there are a few shortcomings, then it is necessary to widen and fill all cracks with the help of a polymer-based repair compound.
- Next, you need to level the height differences.
- After the surface under the concrete is thoroughly cleaned with a construction vacuum cleaner.
- The base of the soil should be compacted to avoid further cracking the floor.
- Next, you need to lay a layer of sand. To create the desired density, take 25% more river sand. It should be wetted and tamped with the help of special rollers.
- A layer of expanded clay or gravel is poured over the sand.
Such training is more common for private buildings.
How to do it yourself?
After the base has been prepared, it is necessary to sequentially install all layers of the concrete floor. Mounting technology has the following steps.
Load calculation
In multi-storey buildings, it is necessary to calculate the allowable load on the floor, before concreting the floor.To do this, you need to find out what material the overlap was made of, calculate the area of the bearing surface and the maximum permissible load on one slab. This result should be multiplied by the index of permissible load. Taking away the mass of the slab from the resulting value, you will find out the allowable load on the floor.
Waterproofing
This layer is necessary so that the concrete base does not absorb moisture and groundwater. Also, the layer helps to avoid moisture in the room, eliminates the appearance of mold and fungi. Among the materials for this procedure, the most popular are a waterproofing membrane or a film of polyethylene with a thickness of 200 microns. The latter must be laid in several layers (unlike other materials).
All parts of the material should be overlapped, equal to about 20 cm. The fastening of these areas is carried out with adhesive tape. It is also necessary to make material lapping on the walls and also attach it with adhesive tape.
The overlap should reach zero.
Thermal insulation
In the process of concreting the floor, it is important to make a thermal insulation substrate.For this layer, materials such as mineral wool, cork coating, polystyrene foam, chipboard, expanded clay, foam plastic, basalt wool. The final thickness of the insulation layer and the place where this layer itself will be located depends on the selected raw material.
For example, if claydite must be placed under a waterproofing layer, then rolled materials are placed on top of it, and plywood, chipboard or carpet - on top of the screed.
Vapor barrier
Next is to make a vapor barrier layer. He is especially needed in a private house. To create it, lags are installed on the waterproofing layer, between which there will be insulation, and then it is treated with antiseptic impregnation. A polypropylene or polyethylene vapor barrier film is applied on top.
If you lay a foil coating as this interlayer, the aluminum side should be directed towards the room. The film should be applied along the wall.. For convenience, the material is cut into strips, the length of which exceeds the length of the lag by 10 cm to make an inlet of 5 cm on each wall.For fixing the coating used glue, double-sided tape or staples.
It is not recommended to strongly stretch the film, because during the installation of the finished floor it will stretch a little.
Reinforcement
One of the most important stages to make the floor more strengthened is reinforcement. For its implementation it is necessary to use a special reinforcing mesh, which can be made of plastic or metal. It can even be made independently using metal rods with a thickness of 3 to 5 mm and a welding machine. When using a soft mesh at the base, it is necessary to fasten the special pins on which it will be attached.
As an analogue, you can take thick reinforcing rods and fasten them together with a metal wire.
Formwork
No less important procedure is the formwork. It is a division of the room into equal rectangular areas that could be filled in at one time. To designate these bases, guides are used, which are fixed with cement mortar. They must be strictly on the same level so that the floor is properly filled.
Formwork should be installed between the guides.
For easier removal of the profile and parts of concrete formwork, it is recommended to lubricate them with oil.
Fill
After the need to pour the mixture. Ready-made compositions immediately poured into the formwork. To manually prepare the concrete mix, you must mix the sand, gravel, water and cement brand M400 or M500. Two parts of sand are thoroughly mixed with 4 parts of rubble, 1 part of cement and 1⁄2 of water in a concrete mixer.
After pouring the mortar into the formwork, the mortar must be carefully leveled with a spade to compact the material and force air out of it. In order to avoid the formation of voids during drying, it is necessary to grind those places where the heavy fractions of the composition have dropped down and irregular areas have formed instead of dried moisture.. This procedure can be carried out a day after pouring concrete.
After decorating the entire room, the concrete should be left for 3-4 days until completely dry. In this case, the surface must be sprayed daily with water to avoid the appearance of cracks.
After that, the guides should be removed and the voids formed should be filled with a solution. To harden the concrete faster, its surface is moistened and covered with a film. In such a favorable environment the final drying of the material will take about 4 weeks. At the same time the surface should be sprayed regularly.
Alignment
When you fill several areas with concrete, you need to align them. This process is carried out using the rule, which is located on two adjacent guides and stretches towards itself. The tool length must be at least 100 cm. For smooth sliding of the rules, it is better to pre-wet it in water. In the process of work, the surplus of concrete will be poured into adjacent areas, and the level of the floor will level off.
Iron
An additional procedure can be ironing. This procedure involves rubbing cement or a special mortar into the concrete surface to increase strength. The cement and sand slurry can be applied with a trowel. As an additional element there is sometimes added liquid glass or limestone dough.
The same components are used in the dry method of ironing, when the mixture is sifted through a sieve and placed on the floor with a layer of 3 mm.Over time, the mixture will become mushy because of the absorbed moisture. It will need to be rubbed into the floor with a trowel until the surface is flat.. Next is the removal of irregularities with the help of skin.
Dedusting
Some carry out such a procedure as dusting. It is an additional protection of concrete surfaces from the accumulation of dust on them. An excellent method is topping coating.. It is a mixture that includes mineral additives, Portland cement, dyes and various other elements.
This solution should be applied in the process of hardening of concrete, mixing it with the top layer.
Finish stage
If various spots of glue and other difficult to remove contaminants remain on the concrete surface, they can be removed by milling.
At the final stage is a coupler. It is a cement mixture, which includes plasticizers. This solution is poured onto the floor and leveled off independently. The screed will dry from 2 to 3 days, but the surface must be wetted with water every day..
Tips and tricks
To make the process of creating a concrete floor without complications, it is necessary to listen to the recommendations of professionals.
- When the concrete dries out after pouring, and the guides are removed, pay attention to the joint between the wall and the floor. Due to material shrinkage, small cracks may form. They can be sealed with sealant.
- You can decorate the concrete screed mosaic elements, if you do not plan to do another finish.
- Fill concrete floors should be away from the angle opposite the door.
If you follow all the rules of laying a concrete floor, as well as take into account various nuances, you will be able to create the perfect concrete cover both in a private wooden house and in an apartment of a brick high-rise building.
How to pour a concrete floor on the ground, see the following video.