Subtleties of choice of cement
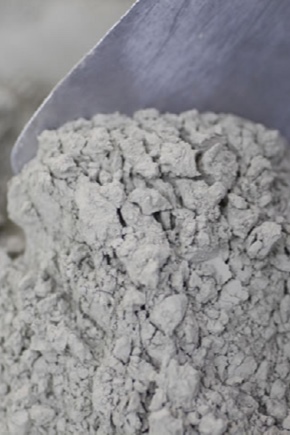
Not a single building can do without cement, and no matter what kind of house is built - brick or wood. The only difference is reduced only to the required amount of the mixture. This building material has been successfully used for more than one century due to its high quality and excellent operational features.
Production features
As soon as people began to build houses, they had a need for such a composition that could hold stones and other building materials together. At first it was ordinary clay, but such dwellings were short-lived, and the building itself looked quite unpresentable.
A little later, the builders discoveredthat the lime mortar also has some binding characteristics - this discovery was made by the ancient Greeks and Romans, and the latter noticed that if volcanic ash was added to the lime, the masonry becomes truly monolithic.
Lime was used in Russia, mixing it with clay and water. At the beginning of the 19th century, a building mixture was created by experiment, which in its parameters is close to modern compositions.
So, cement is the definition of a material consisting of components of clay and limestone. They are mixed with each other and subjected to long-term heat treatment, after which the resulting mass is ground to a powder.
The mixture has a gray tint and, when interacting with water, forms a solution, which upon drying becomes hard as a stone. Its exceptional feature is that mass hardens only in high humidity conditions, and this process can occur even under water. This, by the way, is the main difference between cement and many other binders.
For example, gypsum and air lime gain strength only in air.And as a part of concrete, it hardens not so much because the water evaporates, but rather as a result of its reaction with the powder: at this moment heat is released and solid or crystalline substances are formed. That is why the process of mixing the mixture itself is often called the shutter, and not at all the dissolution.
The monolithic mass is formed due to cement hydration, the concrete should not be dried in the scorching sun - it will simply “tear”, it will crack and very quickly begin to crumble.
To avoid such unpleasant situations and save money, it is recommended to moisten the concrete solution until it is completely dry.
We will dwell a little more on the features of production.
At the first stage, limestone is procured, chalk, marl and lime tuffs are considered the best, but various gypsums and dolomites are not recommended to use - the strength of cement based on them leaves much to be desired. Then the raw material is mixed with clay in the ratio of 3: 1 and the resulting mixture is sent to a rotating furnace, heated to 1400-1500 degrees.
It is this temperature that ensures maximum sintering, at which the components of clay and limestone melt and diffuse among themselves.
After 3-4 hours, the composition leaves the kiln, at this moment it consists of many different-sized lumps - it is cement clinker, then it is crushed to particles less than 100 microns in size, at this stage 6% of gypsum is introduced into the composition - this is necessary for did not absorb moisture from the air.
In addition to gypsum, other active components are added that improve the performance characteristics of cement and allow it to be used in various construction sectors: all additives give cement certain parameters, for example, water-repellent or quick-hardening building materials, and concrete is produced in conjunction with CBC.
Properties and specifications
Consider the basic properties of cement.
Grinding fineness
This parameter determines the rate of hardening of the cement mortar and the strength of the resulting stone. Dependence here is inverse - the less grinding - the faster the process of freezing and the stronger the resulting monolith. Accordingly, the prices for fine-grained cement are higher.
The fineness of grinding is determined using the indicator of the specific surface and the composition of the grains. For this, the material is sifted through an ultrafine sieve, the cell sizes of which do not reach even 8 microns, while the main part of the cement should be easily sieved.
On the other hand, the smaller the grind, the more water is required to dilute the cement. That is why the introduction of both large and small particles in the range from 40 to 80 microns is considered optimal.
To make a quick-hardening type of cement, up to 25% of particles are necessarily added; superfine grinding - they significantly increase its strength and reduce the risk of corrosion.
Corrosion resistance
During operation, water and acid-base solutions have a constant effect on cement stone, which leads to corrosion of reinforced concrete structures. In order to avoid this, special hydroactive materials are introduced into the composition, which significantly slow down, if not completely alleviate the activity of chemical salts, and also contribute to the waterproofing of concrete products.
As a rule, as such, additives based on polymers are used, which significantly reduce the index of porosity of a substance and increase its resistance to adverse external factors.
It is through the introduction of such components that cement becomes a truly durable and reliable material.
Frost resistance
To make high quality concrete it is necessary to use only high-quality cement, since during storage any composition absorbs moisture from the air in micro doses. In freezing temperatures, it freezes and increases in volume by 7–10%, and when repeated several times, it causes serious concrete damage in the future.
In the conditions of constantly growing prices for building materials, the property of maintaining its performance under the influence of low temperatures acquires special value.
Modern cement compositions are designed in such a way as to repeatedly withstand the cycle of freezing and thawing.
In order to achieve good frost resistance, sodium abietat, wood pitch and other components are introduced into pure cement., which cause the resistance of the composition to temperature and increase the durability of concrete as a whole.
Special air-entraining additives are also introduced into the structure, due to which the structure is enriched with air bubbles, they effectively solve the problems of expansion of the liquid during solidification.
Water demand
The physical density of cement grains is several times the density of water,therefore, if it is excessively saturated, capillary forces retain only a fraction of the moisture inside themselves, and the rest is brought to the surface of the mixture. This causes the sedimentation of particles, which, in turn, has an impact on reducing the strength of the entire concrete structure and contributes to its rapid destruction.
The ability of cement to water demand is determined by the amount of fluid needed to prepare the working solution. It is measured in percent, for example, in Portland cement, this figure is 22-28%. If the water requirement is low, then from such a material is obtained more durable and frost-resistant concrete.if this indicator is overestimated, then the materials obtained from the composition will differ in special porosity and will not last long.
Setting speed
Ideally, the solution should set and neither quickly nor slowly. Moreover, the time is affected by additives, as well as liquid volume and air temperature. The adopted standard indicates that the freezing should begin 35–40 minutes after the manufacture of the cement slurry.
For complete solidification, it takes about 10 hours.
Strength parameters
The indicator of the strength of cement is calculated by the method of compression of the sample, which is held for 28 days. When testing cements of various grades, the compressive strength is also different. Modern industry produces cements for which this figure is 300, 600, as well as 700 and 1000.
Many consumers believe that it is strength that is the main characteristic of cement, which must first be paid attention to. This is not so - all the parameters of the composition have the same value and equally affect the strength and durability of concrete structures.
Kinds
There is no official classification of cements. In the most general terms, several groups of compositions can be distinguished, the criteria of which are based on various parameters.
So, depending on the destination composition emit general construction and special compositions. If the composition is taken as a basis, then it is possible to designate variants with additives and pure cement.
If we classify cement depending on the rate of hardening, the following options are most common:
- quick setting mixtures - those, whose freezing rate is less than 45 minutes;
- normal setting - harden within 45–120 minutes;
- slow hardening - freeze over 2 hours.
Also isolated stress, fire-resistant, self-expanding cements and many others.
Let's stop on the most popular types:
- White cement - This is a material that is produced from low-iron clinker that undergoes bleaching. This is a material with unique properties, it can be used not only for bonding surfaces, but also for the manufacture of sculptural elements and columns, as well as for cladding the facade of a building. Due to its color, the use of white cement allows to improve the aesthetic component of the surface. By adding certain pigments, you can get colored cement.
- Waterproof Expandable Cement Is a substance with a high setting and hardening rate. It is produced in the process of simultaneous grinding of cement, gypsum and calcium hydroaluminate. Such cement begins to set already after 4 minutes from the moment of mixing, finally dries in 10 minutes.
This material is widely used for waterproofing seams and their caulking.
- Waterproof non-shrink cement - the basic composition of the components of such cement is the same, however, the processing and production technology makes the rate of hardening even greater - it takes no more than 5 minutes to completely dry the composition. This composition is used to form a waterproofing shell for concrete products.
- Quick hardening portland cement - it is a cement that is quite finely ground, making it more intense than standard portland cement. Material gains particular strength in the initial stage of solidification - after 1-3 days. Most often it is used when carrying out repair work.
- Plasticized portland cement - composition, in the production process of which a 0.25% sulphite-alcohol-based mash is introduced into the clinker grinding, due to which the frost resistance of the mixture and its plasticization increase significantly.
- Hydrophobic cement - made by co-grinding Portland cement clinker and gypsum, as well as the introduction of the axil or other hydrophobic additives.The water absorption of such cement is low, because it can be stored for a long time even in conditions of high humidity and this does not worsen its physical and technical features. This mixture does not form lumps, and the concrete on its basis does not crack with time and does not stratify.
- Aluminous cement - A hydraulic binder that is made from alumina-rich raw materials, usually limestone or bauxite. The material hardens at low temperatures, so it is widely used for repair work in the winter season.
- Magnesia cement - obtained from raw materials rich in magnesium oxide. He found application in the arrangement of magnesian floors.
- Portland cement - it is obtained by grinding portland cement clinker with gypsum and special additives, the burning technology is constructed in such a way that the content of calcium silicates is high in the resulting product.
- Pozzolanic portland cement - these building materials include components of volcanic origin in their structure. This composition quickly hardens both in the open air and in water, while mixtures based on such cement do not give any efflorescence and are highly hygroscopic.As a rule, such material is used when equipping pools.
- Acid Resistant Cement uses in the manufacture of quartz sand and sodium fluoride, this composition is resistant to most mineral and organic acids, it does not change its characteristics in water. However, the reaction with alkalis begins to break down.
Marking
All types of cement have special designations that reflect their scope of use. Marking consists of letters and numbers.
- BOC - Portland cement.
- SS - sulphate-resistant cement.
- ShPC - Portland cement slag.
- Gf - hydrophobic composition.
- BC - white.
- Submarine - plasticized cement.
- VRTS - waterproof.
The degree of strength of the binder is denoted by the letter "M" and the number, for example, M500 - this means that such a material can bear the load up to 50 kg / sq. see. It happens that this characteristic is simply indicated by a number - 22.5, 42.5 or 52.5 - this is not a brand, but a class. It shows that the material can withstand a pressure of, for example, 22.5 MPa.
The letters A and B indicate the number of additional components: A means that their percentage is 6–20%, and B - from 21 to 35%.
Scope of application
Cement is the most popular and popular building material, its scope of application is practically unlimited. It is used in construction at all stages: the construction of the foundation, laying the basement, laying walls, arranging roofs, installing plumbing fixtures, the composition cements floor structures. Using the material, blocks are produced.
The main function of cement is to bond the structural elements of buildings under construction, as well as to align the surfaces of all types. No cement, even the most insignificant repair, can do without cement.
Special consideration deserves the scope of application of specialized cements:
- PC500 - it is widely used for the production of reinforced concrete structures and concrete products, as well as in industrial and civil construction - it is in these industries that the most stringent requirements for hygroscopicity, frost resistance and durability of building mixtures are formed. In addition, cement in this category is often used during emergency and repair work - this is due to the extremely high initial strength of concrete.
- PC500D20 - this compound is widely used in the construction of all types: housing, industrial and agricultural. The material is used for the production of precast concrete structures, various elements of beams and floors.
In addition, this cement is a base material for the cultivation of concrete solutions, which are used during plastering and masonry work.
The main consumer qualities of this cement are frost resistance and high resistance to corrosion, which is why the brand enjoys more circulation than ordinary portland cement.
- PC400D0 - this kind of building structures is required in the manufacture of structures made of reinforced concrete, as well as for the installation of possible underwater and surface structures, which are exposed to a significant impact of mineralized and fresh water.
- PC400D20 - necessary for the production of prefabricated reinforced concrete structures, beams, wall panels and other materials necessary for construction.
Cement is used for arranging country paths, isolating basements and creating a monolithic basement and many other types of work, the scope of its application is wide.
However, each of them requires certain grades and types of cement, therefore it is necessary to clarify in advance all the requirements for the materials used.
Shelf life
The shelf life of any cement is several months. If you follow certain rules, you can use an overdue composition. However, keep in mind that this is permissible only for arranging non-critical structures. Many builders with little professional experience buy cement in large quantities for the future, but this is not quite the right approach.
According to GOST 10178-85, each type of cement has a certain shelf life, it should be especially pointed out that this period is permissible only when creating certain conditions for the storage of material:
- for fast-hardening formulations, packaged in bags or plastic containers - 45 days;
- for general purpose cement, packing in soft containers - 60 days;
- for bulk fast-hardening cement - 45 days;
- for bulk cement - 60 days.
Despite the rather short shelf life of cement according to GOST, in practice it is possible to increase the shelf life of the brands M200, M500, M600, M700 and M400 for six months or even a year.This is possible when a number of conditions are met, namely, the cement is packaged in a holistic soft package and placed in storage in a dry room.
Packed materials should be placed on wooden piles or plastic pallets, while keeping the distance from the pallets to the floor level of at least 10 cm. Then the packages with cement are carefully covered with plastic wrap, and even better each package must be packed in a plastic bag.
If all conditions are met, then the shelf life of cement can be increased to several months. For a better understanding of the consequences of improper storage, let us dwell in more detail on what happens to cement under conditions of high moisture and carbon dioxide that is contained in the atmosphere.
As already mentioned, any mineralized chips and cement composition are hygroscopic substances that absorb moisture well. When moisture is absorbed from the air, the hydration process begins, in which the cement reacts with water and crystalline hydrates are formed as a result. Such materials are absolutely not suitable for use..
In the manufacture of cement, all the basic components of clinker are heat treated at temperatures up to 1000 degrees and above, decarbonization occurs, that is, the starting material is split into lime, carbon dioxide and calcium oxide. The latter, in turn, undergoes a series of metamorphoses, as a result of which strong cement is formed, and carbon dioxide goes into the air.
During prolonged storage, the reverse reaction occurs - carbon dioxide is absorbed by the main components of the cement and, as a result, the strength and performance parameters of the composition are reduced.
Manufacturers
It is difficult to say which brands make the highest quality cement mixtures. The construction market is filled with proposals from a wide variety of domestic and foreign manufacturers, each of which sells compositions of different markings and parameters.
A few years ago, the absolute leader in the cement market was considered Holderbank Concern (Switzerland), it includes enterprises in 70 countries of the world, and the volume of cement produced exceeds 100 million tons - this figure is equal to half of the global production per year.Holderbank manufactures the highest quality cement on advanced technological equipment. All products sold comply with international standards EN 197-1.
However, quite recently the leader has changed. Palm dominated the French manufacturing Lafarge groupwhich has its plants in Europe, Asia and America, and closes the top three CEMEX (Mexico).
Among Russian enterprises, the products of three brands are in the greatest demand:
- Eurocement Group - is the leader of the domestic segment, the production capacity of which includes plants in 16 regions of our country. Users note that the cement of this brand is the best in terms of value for money.
- Novoroscement - This is the second largest domestic producer of cement mixes in terms of sales, its products are sold in the largest construction hypermarkets of various Russian cities by packing 50 kg each.
- Siberian Cement - another well-known manufacturer, who has established a full cycle of cement manufacturing, is one of the three leading Russian manufacturers who put on the market only the highest quality and practical material.
Tips
In recent years, construction has increased dramatically, and the demand for cement has increased. This gave rise to the emergence of a large number of unscrupulous manufacturers who produce cement with the addition of additives that impair its operational properties.
In order not to be mistaken, you should know exactly how good cement should look and what you should pay attention to when purchasing it.
Professionals give some topical recommendations:
- As a rule, cement is sold in bags or in bulk. It is preferable to purchase the mixture in the package, since it was protected from the adverse effects of the external environment at the storage stage and, accordingly, retained its consumer characteristics.
- On the packaging, in accordance with the requirements of the legislation, it is mandatory to place information about the manufacturer, date of issue, GOST. Under the loose cement can be hiding any composition.
- If the cement is purchased in large quantities, then each package should be checked for the date of release, as in the total volume unscrupulous sellers can mix the stale cement, and as already mentioned, the activity of the composition in six months after the release can decrease several times.
- The freshness of the cement can be checked independently - for this you only need to hit the bag with your hand, if the cement is fresh, then the sensations do not resemble a blow to the stone. By the way, the cement in the very corners of the package is first of all hardening, so you should definitely check these areas.
- If possible, make sure that the cement is stored in a dry place with a good level of ventilation.
- Experts recommend to conduct an "experimental" test of cement, for this you need to take sodium bicarbonate water (for example, ordinary Borjomi), release all gas from it and knead cement dough from which to mold small cakes so that the thickness in the center is about 5 cm, and at the edges - 1 cm. High quality cement should begin to harden no later than 10 minutes, and its thickened part should heat up during this time.
If neither the one nor the other happened within half an hour, refuse to purchase this composition.
In the next video you will be able to observe the process of cement production.