Acoustic foam rubber for the ceiling: the subtleties of choice
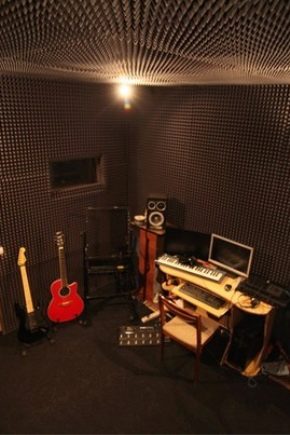
This article will discuss the soundproof ceilings: classification, properties, application, short installation technology of a separate type.
Soundproof ceilings are considered the most effective practical method for eliminating noise in a room. Sound insulation is achieved by reducing the power of the acoustic wave in the insulator.
We will talk about the various types of acoustic ceilings, the various mounting options for these structures.
Types of acoustic ceilings
Sound modules are called the main component of acoustic ceilings, such modules can be assembled in various ways. According to the principle of installation, the system is divided into stretch canvas, suspended ceiling construction, frame or frameless.
The frame type of acoustic embedded structures is equipped with a modular structure: going to the ceiling of separate solid sound insulation plates. But the frame itself is assembled from ordinary battens and profiles of different geometry. The finished profile creates dimensionally suitable cells for the installation of sound insulating plates. Such the frame is usually fixed directly to the ceiling and walls, for fixation, tight gaskets are used, which suppress sound vibrations. There are no solid links in this system.
Frame ceilings, that is, their inner layer is formed by special sound-absorbing panels. It turns out something like a kind of sandwich, inside have sound-proof material, for example, foam rubber. Outside the panel trim a beautiful decorative coating..
To date, developed many different methods that allow you to place the blocks inside the frame. One of the known variations of frame ceiling structures include Armstrong - suspended systems, plates in this embodiment are installed in the upper cells. In such a ceiling construction, acoustic recessed plates to the profiles are usually notare fastened. In the finished frame are installed various acoustic panels that are suitable for the parameters for the cells.
Soundproof frameless panel system consists of facing materials, acoustic embedded sandwich panels. Such built-in acoustics differs from any other systems by the possible fastening of panels directly to the ceiling itself.therefore, there is no need to assemble the frame. This type of fixation is made possible by the integrated fastening element in the modules themselves.
Frameless constructions are insulated with soft wool, creating a kind of air acoustic mats. Outside, the panels are veneered with 12.5 mm gypsum fiber panels, so the material acquires a high level of hardness. The panels are attached to the ceiling through a special vibro-knotted knot. Acoustic type plates are selected for sound insulation parameters.
For example, 40-mm panels perfectly showed their unique characteristics during household use. But the 70-mm modules are used to suppress average noise. 120 mm panels are used in fairly noisy rooms.such as concert halls and cinemas.
Tension type acoustic ceiling is made of PVC film. This material has incredible soundproof qualities. The film is processed in a special way, it allows you to enhance the effect, perforate the film with small holes or complement the anti-noise layer.
A huge number of such holes prevents the penetration of sounds. Noise is slightly damped in these holes. The film is stretched using a special technology, the film is attached to the wall baguettes.
Soundproofing
The soundproofing types of plates are hard or soft, it all depends on the type of insulator used. All acoustic materials have their own characteristic qualities; different acoustic materials are used in different places.
Fiberglass type plates
This material is made from an oblong fiberglass yarn. This thread is laid in the same direction. The size of fiberglass yarns allows you to produce a solid panel fabric of the longitudinal direction. Fibers are bonded with a special polyester resin.
Fiberglass plates are moisture resistant, respectivelyThis material is used as sound insulation for rooms with a high level of humidity. The front, as well as the flip side of coated plates. Decorative facing is made of a special polyvinyl chloride film; it is also made of aluminum laminate and perforated tin.
Acoustic waterproof panels are trimmed with sheet material from glass felt or aluminum foil used. The dimensions of the panels start from 60x60 cm and reach 1.2x1.2 m, while the maximum thickness of the product reaches 100 mm.
For mounting acoustic fiberglass plates use a company frame or some other suspended acoustic cloth with special cells of the desired size. It is possible to fasten the plates with glue or use screws.
Slabs made of stone wool
Such an insulating type of products is made from dolomite, limestone, basalt, the plate is processed according to a specific technology. To achieve an increase in soundproofing qualities, perlite or clay is added to the material. The fibers are bonded with gypsum, starch or latex.Panels, which include more latex, have high water resistance, such products can be installed in rooms with high humidity.
The front surface of the plate is painted in various colors.. You can use another method of decoration, for example, cover the plate with special foil paper.
To improve the sound insulation characteristics, a highly efficient noise absorbing membrane is mounted on the walls.
Tiled material is made from high quality stone wool. The thickness of the product can reach 120 mm. The dimensions of such panels - 600x600 mmThis allows the use of products for other acoustic structures.
Drywall Panels
Often, perforated plasterboard type 595x595 mm with 8.5 mm thickness is used to install sound insulation. At the same time, the front part can be decorated with various materials, the back side of the products is covered with a sound-absorbing layer made of nonwoven material.
The soundproofing characteristics of drywall give the existing holes, which occupy up to 15% of the total quadrature.
Perforated drywall is easier to suppress the low frequency typewaves. The generated echo decreases, while the audibility in the room remains excellent. Sounds spread evenly.
Typically, perforated plasterboard is used in rooms with a moisture indicator of up to 95%. Install drywall panels in a quality system, or use for this purpose various frame ceiling structures with corresponding dimensions in the cells.
Installation
The sequence for mounting the frame sound insulation is followed by examples of the layout of the suspended structure. Installation begins after fixing the nodes directly to the ceiling itself. Such work should be done in conditions of 70% humidity, the temperature in the meantime should be from +15 to -30º.
First you need to check the completeness of the entire speaker system.
Usually this kit is built:
- from acoustic plates, at the same time the size of products is 600х600 mm;
- carrier profile, the length of which is 3.7 cm;
- longitudinal profile 1,2 centimeter;
- transverse 6 cm profile;
- profile wall 3-centimeter with tight elastic pads;
- adjustable custom suspensions;
- metal profiles, where the indicator width of one shelf - 15 mm;
- T-shaped profile and wall L-shaped type.
The assembly of the ceiling structure occurs according to a certain principle:
- Perform markup to fix wall slats. For such work will require the use of water level. Apply a horizontal line under the wall profile should be at the closest distance from each plate, while taking into account the equipment fixed on the ceiling.
- The mark of the location of the carrier rail is applied in the range of 1.2 meters parallel to the wall.
- The markings of the longitudinal profile are applied perpendicular to the marks for the carrier rails, this gap should be 0.6 meters.
- The marking of the transverse profile is applied perpendicular to the longitudinal marks, and the distance between them should be 1.2 meters.
Marking is applied to accommodate the suspensions, which will be located above the support profile at a distance of 1.2 meters, not more than 0.6 meters from the wall. 0.6 meters is rarely done, therefore it is recommended to arrange chess marking. At the same time, the load on the installed hangers should not be exceeded (3.5-6 kg / m²).
For more powerful panels used reinforced type of suspensions.
- Special markings will allow you to accurately calculate the number of suspensions, required rails, mounting plates, it will be possible to determine the size of the modules. If necessary, the profile is cut with a hacksaw.
- Wall type profile is fixed by marking with screws at a distance of 0.5 meters.
- By marking with the help of anchors, the suspensions are fixed directly to the floor panels. It is not necessary to observe special accuracy when fitting the mounting holes. A small slope after eliminate the change in height.
- Next, the carrier profile is attached to the suspensions, they should be leveled in a single plane, using an adjustable type of suspensions. Too long profiles are connected to the floor, and then attached to the installed suspension.
- Next, fix to the already mounted rails all remaining profiles.
- Acoustic plates are installed directly in the cells located in the assembled frame. The plates are tilted up above the false ceiling, and released onto the prepared place horizontally.
- When the panel gets stuck during installation, it is impossible to press it, you can only push it from the corners.To the installed plates with luminaries electrical wires are attached immediately.
- The last plate during installation should be supported with a palm.
In the next video you will find an experiment using acoustic foam rubber.