Brick masonry mixes: types and characteristics
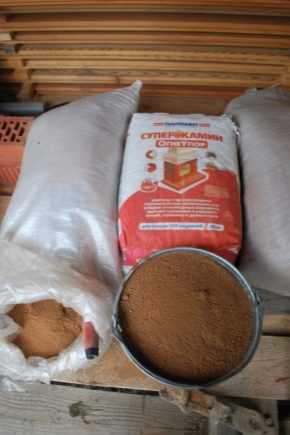
Mixtures for brick masonry stoves and fireplaces are designed not only to fasten building elements, but also to ensure the tightness of the structure. The qualitative composition guarantees a high service life of the stove or fireplace.
Special features
For the construction of furnace and fireplace designs, only fire-resistant brick or natural stone is used. To ensure the monolithic design allows the use of a special mixture for masonry stoves with heat resistance and high strength. In addition, such mixtures are characterized by medium plasticity, the absence of toxins and unpleasant odors when heated.Their peculiarity is that they fill the entire space between the elements without forming voids. This ensures the tightness of the furnace - no disturbing air enters it, carbon dioxide and toxins released during combustion do not escape.
Such compositions can be purchased in finished form or mixed with his own. In the first case we are talking about dry mixtures, consisting of the necessary ingredients in the right amount. Before using them, just fill them with water and mix with a mixer or a special nozzle on the drill until a homogeneous consistency. Independent preparation of the solution involves the purchase of the right ingredients and mixing them in the prescribed proportions. Autographic mixtures are often inferior ready-made in their qualities, since it is not always possible to correctly calculate the required ratio of products, to find the right ingredient.
When it comes to oven blends, professionals appeal with terms such as refractory, heat-resistant and heat-resistant. Despite the similarity, these concepts have different semantics, which should be understood before the beginning of mixing the mixture.
Heat-resistant is a composition that withstands high-temperature heating and at the same time retains its carrying capacity. When cooled, this mixture retains chemical and structural features and is not deformed. The heat resistant version is characterized by mechanical and physical characteristics. But if to speak shortly, it withstands higher temperatures, and can also be used as part of mechanisms.
Refractory is a heat-resistant or heat-resistant composition that can withstand, in addition to high temperatures, the effects of aggressive components contained in flue gases, without loss of strength.
Kinds
Clay compositions are ready and divorced independently. Dry compositions, in turn, are divided into simple and improved. The first variants contain only clay and sand cleared of impurities and are used for aggregates that do not experience sudden temperature jumps. To increase strength, cement is sometimes added to the finished simple mixture. Simple clay compositions differ in price availability. Their heat resistance is about 1100 degrees, fire resistance is 100% (it dissolves only in fluorine-antimony and hydrofluoric acid).This composition is not used for laying outdoor fireplaces and sauna stoves, as it becomes limp at high humidity. When used indoors with a normal level of humidity, this feature is an advantage - if necessary, you can move the stove.
Improved analogues include, in addition to clay and sand, plasticizers, thereby providing increased strength, elasticity, refractoriness of the solution. It is suitable for joints that are subject to sudden changes in temperature and humidity, so it can even be used for outdoor fireplaces. Such mixtures are more plastic, which allows you to form a thin layer, and also have a water-retaining property, so you can refuse to pre-soak the bricks.
Depending on the place of use, the compositions are cement, clay and lime. Cement are cement-sand, with the addition of clay composition used to fill the base of the furnaces. The furnace part, as well as the surfaces subjected to high heating, are erected with the use of clay mixtures (or clay-chamotte), the lining is made with the help of compositions containing lime.In addition, there are universal ready-made products.
The foundation of the furnace is not exposed to heat, so the lime-cement mixture that can withstand a temperature of 200-250 degrees is suitable for pouring it. For the furnace part and elements that are in direct contact with an open flame and exposed to elevated temperatures, a heat-resistant mixture is used. It is also a repair, since the composition is used for the repair of structures and mechanisms that are subject to high-temperature influence.
Heat-resistant solution can heat up to 1300 degrees, while it only becomes stronger. This is due to its composition, which includes clay and chamotte filler. The material has a higher price compared to the price of clay solution. If necessary, increase the strength of the furnace is used cement-chamotte mixture. It has the strength characteristics characteristic of a cement-lime analogue and typical of a clay-chamotte modification with increased heat resistance. Indicators of refractoriness are considered sufficient for heating.
The lime mixture contains lime dough (purchased in a shop,has a finished look) or quicklime lime-pot in the form of pieces. The last one before use should be broken down and extinguished. If even a small amount of burnt grains remains, they will damage the integrity of the seams when heated. Such a composition has a lower heat resistance compared to clay counterparts - about 450-500 degrees, withstands the effect of flue gases. The mixture is non-hygroscopic, therefore suitable for outdoor use. As a rule, lime mortar is used when laying the part of the chimney protruding above the roof. To accelerate the setting of the mixture allows the addition of gypsum. To increase the strength of the used cement.
The advantage of ready-made mixtures is not only ease of mixing and accuracy (adjusted to grams of the contents of the components), but also the ability to choose a product for each type of work - this allows you to fully manifest the characteristics of the mixture and ensure the reliability and durability of furnace designs. Most manufacturers share compositions for structures used indoors and outdoors, and also offer separate modifications for bath units used at elevated temperatures and humidity.
In addition to masonry and plaster mixtures, analogues for pouring the base and repair work, laying the furnace and tile adhesive, also emit trowel mixtures. They allow you to give the finished oven a more aesthetic appearance, to hide small defects in masonry joints. It is important to use special fireproof grout. As a rule, it is sold in devices operating on the principle of a glue gun or foam, and is a cylinder with a thin tube from which the semi-liquid mixture comes.
Product overview of popular brands
To buy the mixture should be from well-known manufacturers, having previously requested the seller certificates of conformity. Among the manufacturers, trusted by experts, there are several brands.
"Borovichi"
Under this brand you can find refractory masonry mixture for the furnace, as well as the solution for chimneys. Professional stoppers often bring in these compositions a clay pulp, which is a clay diluted to a semi-liquid state, which improves the adhesion of the mixture.
ScanEx
Domestic company producing mixes for ceramic bricks under the brand TERM SA, chamotte - TERM TK.The latter are masonry, because they have a refractory property due to the clay-silicate composition. Option for ceramic bricks is cement-sand, so it is only suitable for the execution of the outer walls of structures. Finally, the same manufacturer offers a mixture TERM AL, which is a plaster for exterior walls.
"Plitonite"
The product is German-Russian production. Sold in several versions.
Of the most popular products worth noting the following compositions:
- "Thermal Laying". These are products used for external walls of stoves, fireplaces. Differs in material efficiency.
- "Refractory". The material is intended for heat-resistant bricks.
- "Thermoglue". Adhesive composition for lining the furnace, for example, ceramic tiles.
"Vetonit"
Products of this brand are available in three versions: for chimneys - the SVL series; for combustion chambers, as well as surfaces in contact with open fire, suitable compounds TM; the composition of the elements exposed to ultra-high temperatures (1200-1300 degrees) allows the composition of the TV.
"Terracotta"
Another Russian manufacturer who has received many positive customer reviews.It produces mixtures based on chamotte and kaolin clay, so that the finished product can withstand heat up to 1300 degrees. Differs plasticity, which leads to ease of use.
RATH
Austrian company specializing in the production of heat-resistant refractory furnace mixtures. The high price, according to buyers, is justified by high quality products, ease of application (allows you to put thin seams) and fast drying.
Furnace house "Makarov". It is one of the leading Russian manufacturers, whose products are well known outside the country. The mixtures of this brand are widely used by professional stoppers, which speaks of their high quality. At the same time, due to ease of breeding and elasticity, they can also be used by people who do not have professional building skills. The basis of the composition - varieties of blue and red Cambrian clay.
How to do it yourself?
When mixing the solution for the oven, it should be remembered that each part of it requires a special composition. For example, the underground part is permissible to perform using conventional cement mortar.However, surfaces in contact with an open flame and subjected to heat must contain clay. The mixture for the base is kneaded from cement and sand, taken in a 1: 3 ratio. It is also acceptable to add fine fractional crushed stone to the solution. It should be diluted with water to a consistency resembling wet soil. Sand for the composition is better to take the mountain. Being rough, these grains of sand provide a higher adhesion in contrast to river sand polished with waves.
The mortar sets in half an hour, complete solidification occurs in a day, after which it is possible to perform laying.
Masonry is performed using burnt chamotte clay, which is filled with water and kneaded to the consistency of thick sour cream. It is possible to increase the strength of the masonry joints by adding cement to the mortar, and to accelerate drying by adding lime. When adding cement, 2 parts of clay, 1 part of sand and a third part of cement are taken. Cement should not exceed 10% of the total mixture. Chamotte is a prebaked refractory high-alumina clay, which also includes compounds of the mineral pomegranate and chicory.On sale chamotte can be found under the name "Mortar". It is important that the clay had an average fat content. This indicator can be determined as follows: a ball or sausage should be rolled out of clay, after which it should be squeezed or stretched. If cracks appear on the surface, this means that there is a lot of sand in it - the fat content of such raw materials is low, and it is not suitable for adding to the mixture.
You can also place the rolled ball between two small boards that need to be slowly compressed. The optimum is such a composition in which the cracks on the ball appear only after compressing it by a third. If these phenomena are manifested earlier, then the fat content of the clay is not enough. If cracking is not observed for an excessively long time, then the clay is too liquid. In the case of using lean or overly fatty raw materials, the seams crack and unevenly subside, so it is not suitable for use. In some cases, too fatty raw materials can be corrected by adding sand to it.
Clay need to sift well, removing impurities. For cleansing, you can use the method of experienced stove - the clay is poured into the upper part of the inclined surface with a uniform layer of no more than 30 cm.Down pour water in such a way that it does not reach the clay. Then with a trowel or hands, waves are created that wash the clay. After some time, the raw material remains in the liquid, which is then separated from the water and filtered through a sieve. The next step is soaking the resulting raw material in clean water for 24 hours. After the specified time, the composition is again stirred, if necessary, pour in water.
After that, you need to take five-liter cans, two of which are completely filled with purified clay. The third jar needs only a third to fill with clay, filling the rest with sand. The next jar should contain even less clay - the fourth part of it, and the remaining parts are also covered with sand. The last bank should contain only sand.
The next step is to mix the dry ingredients from all the cans and pour them with water. Knead the composition more convenient hands. The consistency of it should resemble sour cream and not stick to your hands. Professional craftsmen usually check the strength of the composition by rolling a ball about 5 mm in diameter from it. Then the ball is completely dried (about 10 days), after which it is dropped from a height of 1 m.If the ball does not crumble and does not deform, then the composition is considered durable and of high quality.
If there is no time to wait for the clay ball to dry out, then you can fasten two bricks with the prepared mortar. After that, you should wait 5 minutes and raise the bricks by the upper part - the lower brick should not fall or “crawl”. High-quality mixture withstands several such elevations.
The furnace is usually plastered using a mixture based on lime and water, and gypsum or cement is also added to increase the strength characteristics of the layer. Lime is pre-sieved, breaking up lumps. Then all the dry ingredients are thoroughly mixed and filled with warm water. The resulting solution in its consistency should resemble thick sour cream. When it is assumed that the plastered surfaces are strongly heated or the facing composition is used from inside the furnace, then silicon glue is put into it, which provides heat resistance. This additive is usually bought in a specialty store - it is better known as liquid glass. In the finished solution, its content should be less than 20%.
The recipe with liquid glass can look like this: 3 parts of clay and sand are combined with 1 part of liquid glass and the same amount of tooth powder.
The traditional plaster recipe includes 1 part lime, 2 parts sand, and a tenth asbestos. You can get a more durable composition, taking the same amount of sand and cement (together they form 1 part), add 2 parts of sand and a tenth of asbestos. If necessary, facing the furnace with tiles, the following composition is prepared: 1 part of clay-cement mixture (consists of equal amounts of clay and cement), 2 parts of sand. Sometimes table salt is added, which provides an increase in strength properties and prevention of cracking of the seams.
Some masters refuse to add clay to the solution, mixing the composition of cement, salt and sand. The ingredients are taken in equal amounts. However, for this mixture, the tile should be soaked in water for about 2 hours in advance. Strengthen adhesion and prevent tacking off the tiles allows the deepening of masonry joints.
Instructions for use
Ready solutions should be poured with the volume of water specified by the manufacturer, and mix with a mixer or use a nozzle on a drill. Mixing with tools is necessary because it is difficult to do it manually, which makes it necessary to add more water to the composition. This, in turn, contributes to the change in the characteristics of the mixture.The amount of preparation of the mixture should correspond to the amount of work that can be completed within an hour, therefore, it is better to prepare it in small portions. It is unacceptable to add water or other solutions to the frozen mixture to re-knead it.
Dry ingredients are poured into warm water, thoroughly mixed, after which the composition should be left to rest for an hour. The consistency should get a mixture resembling thick cream. If it breaks, you should add water. If, when raking a compound with a trowel, a trace of it remains on the surface, then there is too much liquid — when raking the solution with a trowel to the side, it should keep its shape well and not tear.
When using ready-made solutions, it is possible to not additionally soak the bricks, since dry mixtures are characterized by water-holding capacity, due to which it is possible to shorten the time of installation of the furnace and reduce the time for masonry drying.
The solution is applied with a trowel 10-12 mm thick. Dry mixes allow you to form a thin (from 2-4 mm) seam, which allows you to avoid cracking it, save the composition and get a more attractive result.Work should be at a temperature of from +10 to +35 degrees Celsius. Store the composition should be undiluted, in a sealed original packaging, in a dry and warm place.
Useful tips from the pros
Despite the fact that manufacturers of ready-made mixtures indicate the required amount of water, its volume depends on the temperature of the room. At elevated temperatures of the room, a little more water is required, and at low temperatures (within the normal range, but not below +10 degrees), a little less. Experienced stove-makers sometimes add salt to the refractory mixture, which makes it possible to increase the strength of the seam. 150 grams of salt is taken for 10 kg of dry composition. Instead of salt, 1 kg of cement can be added to the same volume of the solution - the M400 grade will be sufficient.
It is recommended to choose different compositions for the fireplace, due to the difference in their design and operation. Elements of the fireplace heat up less (in fact, only the furnace part is exposed to high temperatures), therefore, the increased heat resistance is not needed here, but strength and moisture resistance are important. In this regard, for fireplaces, experts recommend diluting lime-cement mortar, and for the furnace - a clay-chamotte composition.
After 3-4 days after stoving the oven using dry mixes, you can start heating the device. This should be done actively for another 3-4 weeks, after which you can produce lining. If, after a trial heating of the furnace, in the area of the seams, efflorescence has formed (which is considered normal), then they can be removed with a damp cloth after the furnace has cooled.
To learn how to prepare a mixture for laying bricks, see the following video.