Dry mixes: choose repair compounds for screed
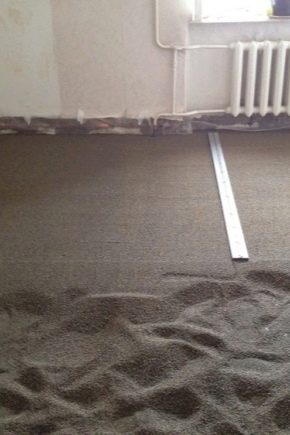
Floor screed, performed under the finish coating, is designed to warm and level the floor surface. In addition, it improves heat and sound insulation performance. To obtain a high-quality solution, you should take a responsible approach to its preparation; therefore, it is much easier and more convenient to use ready-made dry mixes.
What it is?
Dry mixes for construction work are factory-made compounds in which polymeric or mineral (and sometimes both components) binders and modifiers are present. Such a putty for the floor greatly simplifies and shortens the installation work,since to prepare the solution, it is enough to dilute it with water in a certain proportion and mix with a mixer.
Surfaces created with the use of dry blends are distinguished by their strength and durability. In addition, thanks to the additives in the composition, such a composition may have additional qualities - increased frost resistance or moisture resistance, reduced setting time.
The mixture, based on the destination, includes all the necessary components, the volume and proportions of which are met to the nearest milligram.
The active ingredients are as follows:
- binding substances of mineral origin;
- polymer-based modifiers;
- substances that regulate the rheological (stabilizing) ability of the solution;
- aggregates (not clay, thoroughly cleaned sand, expanded clay and other components of different fractions);
- components that determine the speed of setting;
- additives that provide frost solution.
Each of the components provides one or another characteristic of the mixture, so that as a result of this interaction, unique mixtures are obtained for a particular type of work.
Ready-made lime often acts as a mineral additive in the mixture, which, to all other merits, has antifungal effect. In the role of the binder component, in most cases, gypsum, Portland cement, anhydrite, polymer-based dispersing powders, white cement are used.
One of the features of the mixtures is the simplicity of their application. They form an even coating filling the cracks due to its fluidity. Plasticizers present in the composition make it possible to provide the latter; in most mixtures, this is C-3. Its presence makes it possible to achieve fluidity and plasticity of the mass, without resorting to the additional addition of water to the solution.
To avoid stratification of the composition after application and, as a consequence, reduce its strength, allows the presence of water-retaining components in the composition. As a rule, they form a rich foam when in contact with water, therefore they are added together with defoamers.
Modern dry mixes are not inferior in their operational and technical characteristics of the usual cement-concrete analogues, and sometimes surpass them in a number of parameters.
The advantage of ready-made compositions can be called:
- simplicity of preparation - there is no need to measure the volume and proportions of the components;
- most dry mixes are lighter compared to cement-concrete mortar, which facilitates the process of transportation and installation;
- the use of the finished product does not require the involvement of expensive special equipment (for example, concrete mixers), which greatly simplifies pouring and reduces the cost of work;
- the use of dry mixtures allows you to make a coupler with a thickness of even 5 mm, while in its strength properties it will not be inferior to 20 mm concrete screed;
- the ability to choose a composition with the desired prevailing properties (for example, increased moisture resistance, improved thermal insulation, etc.), due to the introduction of special additives in the composition that are responsible for one or another characteristic of the mixture;
- the majority of dry mixes have shortened time for hardening of the screed, while for a concrete analog it is always at least 4 weeks;
- the ability to use a screed, even without having professional building skills - mixtures are characterized by plasticity, fluidity, and have the ability to self-level.
Types and specifications
Depending on the type of binder, the product is divided into:
- cement formulations;
- analogs based on gypsum.
The former are composed of fine cement, and both organic and inorganic components act as fillers and additives. There must be plasticizers.
Cement compositions, depending on the purpose and purpose of use, may have the following modifications:
For roughing screed
Characterized by the filler of a larger fraction. This may be granite chips or expanded clay, which allow you to raise the floor level by 3-4 cm. However, the rough mix does not allow to achieve perfect smoothness and evenness of the coating, therefore a layer of the mixture for the finishing screed is laid over it. Draft and finish composition poured on top of it is optimal for laminate, wooden floor, floor under linoleum or carpet.
You can fix a tile to a rough tie or use it as an independent floor on the street (floor of a porch, verandas, etc.). The thickness of the fill is usually 30-80 mm.
Of course, alignment is also possible with large differences in height with the help of a rough tie, however, in this case, the mixture consumption increases excessively.It is much more profitable to use other methods of alignment with differences in more than 80 mm.
For finishing screed
Reception of the most equal and smooth basis on which the floor covering can keep within, provide fine components and plasticizers. In order to increase strength, reinforcing fibers are sometimes introduced into the composition. In most cases, a layer of 1-1.5 cm is sufficient to obtain the required coating, the minimum thickness is 0.5 cm.
Glue
Can be used on top of subfloor instead of topcoat. Designed for gluing to the screed floor tiles, as well as reinforcing and insulating materials for the subsequent finishing floor.
Self leveling
Characterized by the presence of a very small (no more than 0.3 mm) filler. Also in the composition there are components that provide self-leveling properties of the mixture. For a smooth and durable base, a thickness of 0.5 cm is sufficient. The presence of special components that accelerate the setting speed of the screed allows you to walk on the base 6-8 hours after pouring.
Thermal insulation
Such mixtures are usually used under the "warm floor" system, since they have high rates of thermal conductivity and fluidity.
Gypsum mixes differ from cement mixes in higher drying rates and affordability. They are characterized by antibacterial, heat and sound insulation qualities, do not create dust during operation, and are environmentally friendly.
The basis is a finely divided filler, which is combined with mineral fibers. The latter provide the strength of the solution. Gypsum mixtures are not suitable for outdoor use, and are not used in rooms with high humidity levels.
However, due to the ability to take away excess moisture and give it away if necessary, gypsum compounds are optimal for wooden surfaces. Last under a layer of gypsum screed does not crack and do not rot. Gypsum mixtures are more elastic, but have a higher hardening rate and set faster than cement.
Today there is another version of the screed, the so-called dry. Its use does not imply the use of concrete, so the resulting layer is immediately ready for use.Undoubtedly, the advantage of the product is practicality, ease of use, the ability to reduce installation time.
The dry mixture is not diluted with water, but immediately filled up on the floor and leveled out by beacons. On top of it are stacked OSB or gypsum-fiber sheets on which the flooring is mounted.
Such mixtures are suitable for floors made of wood and concrete, as well as under the system of underfloor heating, due to the presence of plasticizers in the composition. They do not allow air voids to form, due to which the thermal conductivity of the screed increases.
In a separate group should also highlight the mixture for waterproofing. For a long time, waterproof mastic on a bitumen base was used for this purpose, but the use of dry mixtures demonstrates greater reliability and durability of protection.
Waterproofing mixtures withstand a large number of cycles of freezing and defrosting, and also have improved strength properties, which allows them to be used as a screed under the ground.
The compositions are divided into film and penetrating. The first (such a screed is also called a “screed”) form a screed on the surface, while the second solution not only forms the surface layer, but also penetrates into the thickness of the material.Due to this, it is possible to provide capillary waterproofing, which significantly increases the protection of working surfaces.
As a rule, the basis of waterproofing compounds is cement or Portland cement, which provides high-quality adhesion to any type of base.
Depending on the size of the incoming aggregates, the compositions are mortar, concrete and dispersed. Mixtures with coarse aggregates are used for roughing, small fraction (almost ground into dust) - for finishing. The smallest dimensions of the components have self-leveling compounds.
Characteristics of dry mixes are determined by the characteristics of their composition and purpose. In general, they are distinguished by higher water retention abilities in the range of 98-99% (for comparison, the same indicator in cement-sand mortar is 90-93%). This value indicates the ability of the solution to absorb water during the pouring process. Excessive absorption of dry components of moisture leads to delamination of the solution and reduce its strength. Due to the water retention of ready-made solutions of 98-99%, their delamination is only 1-2% (for home-made solutions, this figure is 10%).
Due to the presence of special components, it is possible to achieve the best adhesive abilities of the finished mixtures. They demonstrate good adhesion with most working bases (concrete, wood, brick) and provide greater strength and durability of subsequent finishing coatings.
Unlike home-made cement-sand mortars, dry mixtures are more plastic, fluid. This not only provides a simpler application, but also a uniform coating of surfaces of even complex shape, as well as the absence of air gaps that reduce the thermal insulation and strength properties of the screed.
Purpose
The general purpose of dry mixes for screeds is the organization of the surface on which flooring becomes possible. The narrower "specialization" of mixtures is determined by their composition. Allocate products for rough alignment of the floor, as well as analogues for the final coating, forming a smooth and even coating.
The resulting floor can be used in buried under the soil and prone to increased moisture and flooding surfaces - the so-called compositions for waterproofing.
There is a variety of flooring adhesives. These compounds do not have the ability to level height differences, but provide improved adhesion of the flooring and screed.
Finally, some manufacturers produce universal formulations that are suitable not only for the floor, but also for the preparation of walls, for example, for further reinforcement, plastering, as well as for sealing joints.
The use of ready-made mixtures can not only carry out repairs, but also apply the compositions during the construction phase.
Browse popular brands
Experts recommend to buy dry mixes only from well-known brands and carefully study the attached documentation, as there are too many in the market of counterfeit products. Among the reputable manufacturers who have won the trust of customers, there are the following brands:
Knauf
The most famous German manufacturer of various building mixtures. The range includes both cement and plaster based compounds.
For the organization of the screed, you can choose a cement mixture "Ubo"with improved thermal insulation properties. This was achieved through the use of polystyrene granules.When using this filler, the resulting products are characterized by durability, enhanced heat and sound insulation properties.
Another line for the floor of the same brand - "Boden". It includes products with various numerical designations. For example, "Boden 15" is a composition for forming a superfine layer with a thickness of 2-15 mm. "Boden 25" is filled with a thicker layer and allows leveling the surface height differences of up to 30 mm. When you want to prepare the floor with large differences in height, the manufacturer suggests using a mixture of "Boden 30". With its help it is possible to apply a layer up to 80 mm.
Ceresit
Under this brand is made several mixes for the floor. For example, "Ceresit CN 80", which can be poured with a thickness of up to 80 mm. And you can walk on the flooded surface after 8 hours.
The product "Ceresit CN 808" is considered superstrong, and also differs in the increased wear resistance. This allows it to be used inside and outside buildings, as well as to operate even without topcoat.
The universal action is characterized by the “CN 175” coupler, which is presented as a self-leveling mixture. Fill thickness - up to 60 mm.
"Founds"
One of the leading domestic manufacturers of building mixtures. To fill the floor should purchase the composition "Startoline 41" and "Mixline T-44." The first is recommended for combination with heated floors. The second can be applied with a thick (up to 150 mm) layer. This can be done manually or using special equipment.
Volma
Russian manufacturer, whose history begins in the 1940s. Over the past period of existence, the company has developed many unique formulas, special criteria for evaluating and controlling product quality. Mixtures for the floor include 5 items. For roughing the inside and outside of the premises produced "Volma Rovnitel rough" of cement, lime and sand, with the addition of synthetic components and fibrovolokon. Differs in the increased durability, wear resistance, approaches under a heat-insulated floor.
Volma Bulk Arena is also suitable for thicker screeds, but it is more fluid. The scope of application of the composition "Volma Nivelir Express" - exclusively internal heated objects with normal moisture levels. This mixture is based on gypsum, which is suitable for both draft and finishing fillings, and is also compatible with the “warm floor” system - it serves as a heat-retaining screed.
Volma Nivelir Top is used in cases where an ultra-thin screed is required, as well as increased operating loads, including high humidity. Coating thickness can be 3-20 mm.
Volma Level Comfort also allows you to achieve the finest possible screed. Used only indoors.
How to choose?
As already mentioned, the stated technical characteristics are demonstrated only by the high-quality blend of the original production. It is important that it is not expired, otherwise the operational properties of the product are lost. It is necessary to evaluate the shade of the material - it should not be rich yellow or brick, reddish. This suggests an excessive amount of sand and even clay in the composition.
It is possible to choose the most optimal composition only considering the scope of its application. So, even the highest quality plaster mix is not suitable for floor screed in the pool or washing, as well as for outdoor work.
The higher the load on the floor, the higher should be the indicators of strength and wear resistance of the mixture and the thicker the layer of screed. With a noticeable height difference, it is more logical to purchase a product for rough alignment. It contains coarse grinding ingredients. On top of it, you can pour analogues for the finishing screed. Filling of small-fraction mixtures with a thick layer (above 20 mm) is not rational, as their consumption increases.
For screed under the electric floor heating is recommended to use compounds with fiberglass. It is desirable that the mixture was designed and compatible with the floor heating system. Consider the type of surface. So, for working bases from wood it is better to choose a plaster or dry mix. They will allow for a long time to preserve the structure of the wood.
Tools for work
One of the features of the use of ready-made mixtures is the ability to refuse to engage in the work of a concrete mixer or other special equipment.
The composition is kneaded in a suitable container. In addition, you will need a mixer or drill with a nozzle for mixing. Such a mixer is obligatory, because it will not be possible to manually achieve a homogeneous mixture You can also purchase a special mixer for mixing the dough solution.
Level the floor allow levels.You should not save on them, because the final result of the fill depends on it. The most accurate, and in addition - laser levels are considered convenient and easy to use.
The use of beacons, as well as the rules for leveling the filled solution, allow achieving the same thickness of the screed over the entire surface. It is better if the latter is made of aluminum (such products have low weight and resistance to corrosion). The rule can be rectangular, complex or double-sided. You can smooth out minor irregularities with a trowel or an easier to use plaster grater.
If the solution does not require the entire bag, but only a part of it, do not dispense with the dispenser. Dispenser for bulk and liquid products allows you to accurately measure the required amount.
Required calculations
Simple calculations will help you figure out how many bags of dry mix you will need for a tie. First of all, it is necessary to calculate the volume to be filled. To do this, the area of the room should be multiplied by the value of the thickness of the screed.
The coefficient obtained should be multiplied by 0.1, and then divided by the number indicated on the package as a mixture consumption per 1 m2 with a screed thickness of 10 mm.The result is the total number of kilograms of the mixture, which is required for work. Now, considering how many kilograms of bags are packaged (25 or 50 kg), you can calculate the required number of bags of material.
The required amount of the mixture can be calculated a little differently. To do this, it is first calculated how many kg of the mixture is required per 1 m2 for screeding the required thickness. Material consumption, as already mentioned, with a layer thickness of 10 mm is usually indicated on the package. In most cases it is 20 kg.
Imagine that you need to fill the floor with a thickness of 3 cm. We multiply 20 by 3, we get 60 kg. This is exactly how much dry mix is required to create 1 m2 of screed with a layer thickness of 3 cm. Now we need to calculate how much material is needed to fill the entire room. Suppose that its area is 10 m2. Multiply 60 by 10, we get 600 kg. This is the total mass of the mixture. If the product is packaged in bags of 50 kg, then 12 such bags are required (600 divide by 50), if 25 kg each, then 24 bags.
The calculations do not take into account the volume of water. Usually, 1/3 of the total amount of the mixture of water is required for 1 m3 of solution.
Instructions for use
In general, pouring a screed using dry does not differ from similar actions using a concrete solution.First of all, it is necessary to prepare a working base - clean and dust it. Then determine the level, install the beacons, then pour a tie on them, align it if necessary.
The main difference is in the technology of preparation of the solution. Mixtures do not imply the addition of components other than water. It is important to follow the manufacturer’s instructions.
The composition is poured into a clean, dry container of suitable volume, after which the required amount of water is added to it. The composition is stirred by a mixer, in its absence, you can use a mixing nozzle on a drill.
After the mixture has a uniform consistency, it is allowed to stand for 2-3 minutes (or the amount of time that the manufacturer indicates), and then knead again.
It is important to remember that the ready-made mixtures quickly freeze (usually within 40-50 minutes, and plaster - sometimes faster). To avoid irrational consumption of the composition helps mixing it in small portions. The diluted volume of the solution should be enough to have time to pour the screed and level it before it hardens.
In this case, the next section should be poured as quickly as possible, and also strive to make a minimum of "seams". This is the only way to guarantee the solidity of the screed.
If the solution began to thicken before setting, specified by the manufacturer, it should be mixed periodically. Do not add water.
For more recommendations on pouring floor screed, see the following video.