Features of foam
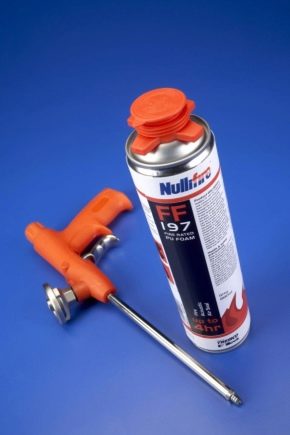
During construction and repair, various materials and structures are widely used. But the same works invariably give rise to a mass of gaps and recesses, holes, especially if the repair is capital. The solution in many cases is the use of an insulating foam, the choice of which should be approached as carefully as possible.
Special features
Polyurethane foam has become such a widespread attribute of modern construction and repair that it is hard to imagine how they once worked without it. Cylinders with easily blown and instantly swelling reagent provide:
- heat insulation;
- sound suppression;
- vibration suppression;
- sealing joints and joints;
- overlapping slots;
- saturation of inaccessible cavities.
Polyurethane prepolymers are displaced from the cylinder by a special gas.The initially ejected substance is light and saturated with small pores. But inevitable contact with air forces the polymerization process and the transition of polyurethane into the form of polyurethane foam. Simultaneously with the chemical transformation, the foam also changes physically; it takes up more and more space, hardens and hardens. This unique substance is extremely useful, but to achieve success, you should carefully examine its technical characteristics.
The key parameters of any foam are:
- displacement of the mixture (figures given on the cylinder refer to the ideal situation);
- expansion level on exit;
- re-expansion (experienced by the substance in the polymerization process);
- the number of pores;
- adhesion to surfaces;
- viscosity.
It has long been known that polymerized foam can take many times more space than the one that just left the factory tank. Inexperienced or inattentive builders often cause serious damage for this reason. First of all, the risk concerns doors and windows, where a considerable weight can put pressure on a relatively thin structure.Professionals know that when the cavity is saturated, it is allowed to immediately send a maximum of 1/3 of its volume there. If voids remain later, this can be corrected by adding additional foam mass, but only after it has hardened.
The density of the foam is closely related to its expansion ratio. The strongest and most stable seams are obtained by using a material with the least secondary swelling. But the downside of this choice is ultimately an increased consumption of the mixture. If the surface of the surrounding structures is quite solid, you can use actively swelling foam in order to save. With regard to the formation of pores, this indicator directly affects the stability of the connection of the foam with other surfaces.
High-quality reagent should have from 88% of clogged pores. Its other valuable property is its excellent adhesion to almost all widely used materials. But It is important to remember that even the best foam does not stick to:
- silicone;
- polypropylene;
- polyethylene;
- Teflon.
Viscosity for practical purposes is also quite important, it is even judged bywhether it will be possible to do the work qualitatively or not. Good viscous foams do not creep down under their own weight and are superbly retained on the treated surface. But there is a nuance: if the temperature is higher or lower than the critical one for this mixture, the viscosity can change significantly. It is possible to compensate for this by wetting the surface to be treated before starting work, in order to increase adhesion. And even better to work at those temperatures that are listed on the package.
Drying time in most cases ranges from 8 to 15 minutes. But still it is recommended not to touch the foam for at least 24 hours. When the surface hardens, it is already possible to cut off part of the layer, to cover with plaster or paint. Normal shrinkage does not exceed 5%, if it is larger, the polymerizing material can be deformed and broken. Then talk about the quality of sealing is not necessary. Additionally, it is worth knowing everything about:
- shelf life and coverage period;
- fire resistance level;
- compression stress;
- coefficient of thermal conductivity;
- shear strength.
Kinds
Polyurethane foam varies greatly depending on the type of concrete composition.Taking the first seen on the shelf cylinder, you can greatly disappointed in the result. Polyurethane foam sealants are divided into two main types: two-component and one-component. Reagents based on a single component are most common. The polymer, when it is sprayed from a balloon, solidifies in about a day.
The exact duration of the freezing is determined by the amount of foam ejected and the atmospheric environment. If you throw too much sealant into the cavity, the distant parts of it will not be able to react with the air and remain liquid. The problem of one-component compositions, unavoidable at the current level of technology, is the short storage time. Unmanaged chemical reactions can start at any time inside the container. Structural or two-component foam is most often used by professionals, its essence - the balloon is divided into two compartments, the boundary between which disappears only at the moment of activation.
The advantage of this reagent is that it can be stored for quite a long time and finally hardens after 20-30 minutes. However, it is impossible to use the mixture in two or more doses.Therefore, two-component foam, as opposed to household foam, is chosen by installers of windows and doors, as well as roofers. And then they need it only in cases where a lot of work is done. In general, to choose a professional option or not depends on many factors.
So, packing of highly specialized foams is made in a container from 0.75 liters, while household cylinders start from 0.3 liters. Therefore, you can focus on the amount of work. In a mass product, a part may remain inside the tank, and in the case of a professional product, this proportion is very small. In addition, it almost does not increase in volume, which allows us to more accurately estimate the need for foam. Twice smaller (up to 3% versus 5-7%) shrinkage also makes the sealant more relaxed and predictable for builders.
But the production of works with professional foam is impossible without a special gun, which is many times more expensive than a standard cylinder. This is fully justified by the increased accuracy of the work performed, which is especially important in the formation of thermal protection and in sealing the seams. Foam is also classified by use. So, the summer product works well at temperatures from +5 to +35 degrees; winter - from -35 to -10 degrees.A universal option is foam that can operate in the temperature range from -10 to +35.
It should be borne in mind that these are just acceptable limits. When the sealant comes out of the cylinder at low temperature, its amount is less than under normal conditions. But after hardening, foam for any season will transfer frost at 40 degrees and heat up to +90. Sometimes on the package proud inscriptions about the "record output" and the like. In fact, this is nothing more than a publicity stunt, because there can be no more than 65 liters per 1 kg of high-grade polymer. And since the capacity of cylinders reaches only 0.95 liters, minus the body, minus displacing gas - the total amount of the product is limited to only 45 liters.
Professionals recommend carefully evaluating the shelf life and appearance of the purchased foam. Any type of sealant during long-term storage unnecessarily hardens and deteriorates. You can assess the quality by shaking the container and holding it in your hand. Something must roll inside, and there should not be excessive lightness. As for brands, here you can safely choose between the most advanced and well-known options.
Heat-resistant and fire-resistant polyurethane foam deservedly stands out in a special category. This material is designed to protect against fire as part of fire insulation. The one-component mixture is initially ready for use, polymerized by atmospheric moisture. In addition to polyurethane foam, it adds special reagents that block the spread of smoke and other gases that occur during combustion. A special kind of sealant does not drain from the verticals and effectively copes with the saturation of any cavities of any kind.
To ensure the highest security, developers are constantly thinking of improving adhesion to metal and glass, brick and cement, wood and polymer surfaces. Much in this regard has already been resolved. In comparison with a simple foam, heat-resistant mechanically stronger, perfectly tolerates the action of moisture (without the formation of mold nests). It lights up more slowly, and under the action of open fire and heat for a long time only swells up, but protects the substrate due to its low thermal conductivity.
It should be borne in mind that even the resistance of the flame and strong heat does not give resistance to ultraviolet radiation.
Big problems are often delivered not only by fire, but also by liquid. Fighting its penetration into certain places helps waterproof type of foam. The necessary properties are given to it by surfactants that form a mass of bubbles. Since less than 10% of all bubbles are open, it is very difficult for liquids to penetrate inside the protective layer. But the problem is that increased protection turns into a significant re-expansion. In addition, hydrophobic foams settle faster than normal, if only there are jerks of temperature.
Important: when sealing joints and parts relating to water, polyurethane that goes outside cannot be cut off. This procedure will improve the appearance, but will violate the integrity of the layer and nullify the protective properties of the coating.
Waterproof foam is completely safe in residential areas, even when it comes to children's rooms and kitchens. It is recommended to specify in advance what are the properties of a particular product. Not always resistance to fire and protection from electric shock meets the required standards.
Waterproofing wet surfaces with foam implies additional cover from above with enamels. On a water resistant product, unlike all other foam mixtures, saving is not recommended. Safety rules when working with him are the same as usual. Pre-perfected technical communications, and only then carry out the final finish. Compliance with these simple requirements is extremely effective and improves the quality of work.
Special mention deserves all season foam. Such a product came into use relatively recently, and not even all leading concerns managed to master its production. The combination of the properties of winter and summer product allows you to use the sealant quite calmly in almost any conditions. But it will still be better if you perform work in the temperature range from +5 to + 30 degrees, this improves the quality of polymerization. Universal foam will be suitable if the gap has a size of from 1 to 8 cm.
Wetting the surface is recommended for cases when the work is carried out in winter. The low humidity of the air, which increases the hardening time, is at least slightly compensated in this way. Water will definitely not become ice if you work quickly and accurately. For any type of sealant, the most attractive humidity ranges from 60 to 80%.
The universal type of foam, due to the insignificant initial expansion, perfectly helps to put brittle and thin structures, to fill up the gaps in easily breaking materials.
Consumption
It is not too difficult to choose a specific type of sealant, but knowing its properties is not enough for a purchase. It is also necessary to figure out how much of the mixture will need to be used in a particular case. Approximate figures are weighted average for the most optimal technological conditions. The slightest deviations in them or in the composition of the sealant lead to a completely different result. It is useful to bear in mind that any consumption standards per 1 m3 are given in the descriptions and in the technical documentation for proper use only:
- on the seam moistened with a spray;
- when sealing adjacent parts with foam;
- by shaking the can before use;
- with the mandatory application of sealant from the bottom point consistently upwards with a laying thickness of 3.5-4 cm in a uniform layer;
- when the manufacturer’s specifications for temperature and humidity are strictly followed.
When the repairman leads a tube or a gun along a certain surface, the exact consumption per meter depends not only on the actual weather.Much means the quality of the foam itself, the use and quality of the dispenser, the professionalism of the workers and the condition of the surface. Even the geometry of the embedded cracks or cavities is of no small importance. If the spray can not be shaken before spraying, it will not emit a light foam, but a viscous, heavy liquid. The total cost of the material will instantly grow, and there is nothing to think about achieving high-quality seams.
Scope of application
In addition to the flow rate, it is useful to know about the nuances of the use of foam in a building (repair) operation. The sealant on the polyurethane base can be used to close any void, crack or seam larger than 20 mm. In addition to sealing gaps in windows, doors, walls and ceilings, this sealing compound can help in other cases. Any use of foam in the room requires careful ventilation during all processing, and ideally, until the sealant completely cures. Foam processing is used if you need to lay and isolate:
- pipelines;
- electric wires;
- other communications.
The porous composition makes the mixture attractive in thermal protection of cooling, heating, plumbing and air-conditioning systems.It is easy to block the cracking in the roofing material with foam, to warm the cold room, to fix certain types of panels and sheets fastened to the walls. Where surface adhesion is low or very precise dosage is required, it is advisable to use a professional grade sealant.
The smaller the pores in the released mass, the better the containment of cold or heat. In addition, lowering the pore size helps to make the foam stronger and more resistant to temperature jumps and to active insolation.
Drying time
Accurately predicting how quickly the foam dries is extremely difficult. But there are a number of common points that cannot be ignored. A key significant factor is the humidity of the environment and the surface. Unlike paint, varnish or enamel, foam dries the faster, the higher the humidity level. After all, it is the process of polymerization, in which water is one of the most important components. Predictably reduced drying time at a significant temperature.
As a result of a series of experiments and observations of practical construction situations, it was found that the polymer precursor solidifies (at a thickness of 50 mm) a maximum of 3 hours.But after that, the process of hardening the polymer itself continues, it will take at least 2-3 times longer. Under adverse conditions (frost and dryness), the total drying time is increased to one day. Therefore, experienced builders are never in a hurry to complete the finishing of surfaces that have been sealed with foam.
Periodic moistening helps speed things up a bit, but no more.
Manufacturers
In order not to endlessly encounter problems after freezing and during the whole period of operation, it is very important to choose the right brand. Rating in Russia is naturally headed by the brand. "Moment". The line of this manufacturer includes a number of interesting options. For example, “Installation” does not require a special pistol for use, and, as the manufacturer claims, all modifications tolerate ultraviolet rays fairly well. There are all-season, and professional, and professional all-season versions, and even a fire-resistant option.
Company Profil offers both pistol and amateur (pipe) solutions. The pistol version comes in a container with a capacity of 0.625 liters. Good market position has Makroflex Standart. This product is easily found in the shops of even the most remote corners of the Russian Federation. Foam adheres perfectly where it is needed, and is distinguished by minimal re-expansion.
Tips and tricks
When using polyurethane foam, many subtleties are found that are not written about on the manufacturers' websites and in the accompanying instructions. Or they write, but many people unreasonably ignore these instructions. If the tool is planned to be used in severe frost, it is better to warm the balloon by putting it in warm water. The optimum warming is up to 5 degrees. In case of emergency, you can cut off the excess foam mass one hour after application.
You can improve the quality of waterproofing, if you pre-treat the surface with a grout. The same compositions as for protection against moisture can be applied to sound insulation in any room. Removing excess portions of the substance helps rags, but it is better to avoid smearing the foam. Hardened surpluses are cleaned with any solvent. The assembly foam which has fallen on hands is cleaned with water solution of table salt, laundry soap or vegetable oil.
Contamination of hands is prevented by elementary, you only need to wear protective gloves. It is important to understand that the foam mass alone cannot solve all sound problems in a room. A comprehensive elaboration of protection measures will be required, but to seal the gaps and holes it is the sealant that is the best choice. Often people are interested in whether expired foam can be used. The answer is negative - there may be a bad yield, and loss of valuable qualities, and excessive shrinkage, and incomplete polymerization.
Review the recommendations on the use of foam in the following video.