Mélanges de maçonnerie de brique: types et caractéristiques
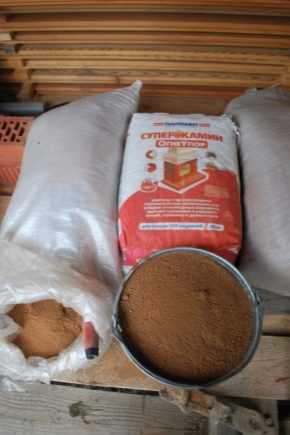
Les mélanges pour les poêles et les foyers en maçonnerie en brique sont conçus non seulement pour fixer les éléments de construction, mais également pour assurer l'étanchéité de la structure. La composition qualitative garantit une longue durée de vie du poêle ou de la cheminée.
Caractéristiques spéciales
Pour la construction de fournaises et de foyers, on utilise uniquement des briques résistantes au feu ou des pierres naturelles. Pour assurer la conception monolithique permet l'utilisation d'un mélange spécial pour les poêles de maçonnerie avec une résistance à la chaleur et une résistance élevée. De plus, ces mélanges sont caractérisés par une plasticité moyenne, l'absence de toxines et des odeurs désagréables lorsqu'ils sont chauffés.Leur particularité est qu'ils remplissent tout l'espace entre les éléments sans former de vides. Cela garantit l'étanchéité du four - aucun air gênant n'y pénètre, le dioxyde de carbone et les toxines libérées lors de la combustion ne s'échappent pas.
De telles compositions peuvent être achetées sous forme finie ou mélangées avec les siennes. Dans le premier cas, nous parlons de mélanges secs, composés des ingrédients nécessaires en quantité suffisante. Avant de les utiliser, il suffit de les remplir avec de l'eau et de les mélanger avec un mélangeur ou une buse spéciale sur la perceuse jusqu'à l'obtention d'une consistance homogène. La préparation indépendante de la solution implique l’achat des bons ingrédients et leur mélange dans les proportions prescrites. Les mélanges autographiques sont souvent de qualité inférieure dans leurs qualités toutes faites, car il n’est pas toujours possible de calculer correctement le rapport requis de produits pour trouver le bon ingrédient.
En ce qui concerne les mélanges pour four, les professionnels font appel à des termes tels que réfractaire, résistant à la chaleur et résistant à la chaleur. Malgré la similitude, ces concepts ont une sémantique différente, qui doit être comprise avant le début du mélange.
Résistant à la chaleur est une composition qui résiste au chauffage à haute température tout en conservant sa capacité de charge. Une fois refroidi, ce mélange conserve les caractéristiques chimiques et structurelles et ne se déforme pas. La version résistant à la chaleur est caractérisée par des caractéristiques mécaniques et physiques. Mais si vous parlez brièvement, il résiste à des températures plus élevées et peut également être utilisé comme mécanisme.
Réfractaire est une composition résistante à la chaleur ou résistante à la chaleur qui peut supporter, en plus des températures élevées, les effets des composants agressifs contenus dans les gaz de combustion, sans perte de résistance.
Espèces
Les compositions d'argile sont prêtes et divorcées indépendamment. Les compositions sèches, à leur tour, sont divisées en simples et améliorées. Les premières variantes ne contiennent que de l'argile et du sable débarrassées de leurs impuretés et sont utilisées pour les granulats ne subissant pas de sauts de température soudains. Pour augmenter la résistance, du ciment est parfois ajouté au mélange simple fini. Les compositions d'argile simples diffèrent par la disponibilité des prix. Leur résistance à la chaleur est d'environ 1100 degrés, leur résistance au feu est de 100% (elle ne se dissout que dans le fluor-antimoine et l'acide fluorhydrique).Cette composition n'est pas utilisée pour la pose de cheminées extérieures et de poêles de sauna, car elle devient molle lorsque l'humidité est élevée. Lorsqu'elle est utilisée à l'intérieur avec un niveau d'humidité normal, cette fonctionnalité est un avantage - si nécessaire, vous pouvez déplacer le poêle.
Les analogues améliorés comprennent, en plus de l'argile et du sable, des plastifiants, offrant ainsi une résistance, une élasticité et une réfractarité accrues de la solution. Il convient aux joints soumis à de brusques changements de température et d'humidité. Il peut même être utilisé pour les foyers extérieurs. De tels mélanges sont plus plastiques, ce qui vous permet de former une couche mince, et ont également une propriété de rétention d'eau, de sorte que vous pouvez refuser de pré-tremper les briques.
Selon le lieu d'utilisation, les compositions sont du ciment, de l'argile et de la chaux. Le ciment est constitué de sable et de ciment, auquel on a ajouté une composition d’argile utilisée pour remplir la base des fours. La partie du four, ainsi que les surfaces soumises à un chauffage important, sont construites à l'aide de mélanges d'argile (ou d'argile-chamotte), le revêtement est fabriqué à l'aide de compositions contenant de la chaux.De plus, il existe des produits prêts à l'emploi universels.
Les fondations du four n'étant pas exposées à la chaleur, le mélange de chaux et de ciment pouvant supporter une température de 200 à 250 degrés convient à son coulage. Pour la partie du four et les éléments en contact direct avec une flamme nue et exposés à des températures élevées, un mélange résistant à la chaleur est utilisé. C'est aussi une réparation, car la composition est utilisée pour la réparation de structures et de mécanismes soumis à l'influence de températures élevées.
La solution résistant à la chaleur peut chauffer jusqu’à 1300 degrés alors qu’elle ne fait que devenir plus forte. Cela est dû à sa composition, qui comprend de l’argile et du mastic de chamotte. Le matériau a un prix plus élevé par rapport au prix de la solution d'argile. Si nécessaire, augmenter la résistance du four à l'aide du mélange ciment-chamotte utilisé. Il présente les caractéristiques de résistance caractéristiques de l'analogue ciment-chaux et typiques de la modification argile-chamotte augmentant la résistance à la chaleur. Les indicateurs de réfractarité sont jugés suffisants pour le chauffage.
Le mélange à la chaux contient de la pâte à la chaux (achetée dans un magasin,fini) ou de la chaux vive en forme de morceaux. Le dernier avant utilisation doit être décomposé et éteint. S'il ne reste qu'une petite quantité de grains brûlés, ils endommageront l'intégrité des coutures une fois chauffés. Une telle composition a une résistance à la chaleur plus faible que celle de l’argile (environ 450-500 degrés) et résiste à l’effet des gaz de combustion. Le mélange est non hygroscopique et convient donc à une utilisation en extérieur. En règle générale, le mortier de chaux est utilisé lors de la pose de la partie de la cheminée dépassant du toit. Accélérer la prise du mélange permet l'ajout de gypse. Pour augmenter la résistance du ciment utilisé.
L'avantage des mélanges prêts à l'emploi est non seulement la facilité de mélange et la précision (ajustée en grammes de composants), mais également la possibilité de choisir un produit pour chaque type de travail. Cela vous permet de manifester pleinement les caractéristiques du mélange et d'assurer la fiabilité et la durabilité des conceptions de fours. La plupart des fabricants partagent des compositions pour des structures utilisées à l'intérieur et à l'extérieur, et proposent également des modifications distinctes pour les unités de bain utilisées à des températures et à un taux d'humidité élevés.
Outre les mélanges de maçonnerie et de plâtre, les analogues pour le coulage de la base et les travaux de réparation, la pose du four et la colle à carrelage émettent également des mélanges à la truelle. Ils vous permettent de donner au four fini un aspect plus esthétique et de masquer les petits défauts des joints de maçonnerie. Il est important d'utiliser un coulis ignifuge spécial. En règle générale, il est vendu dans des dispositifs fonctionnant sur le principe d'un pistolet à colle ou d'une mousse. Il s'agit d'un cylindre à tube fin d'où provient le mélange semi-liquide.
Vue d'ensemble des marques populaires
Pour acheter le mélange doit provenir de fabricants connus, ayant préalablement demandé au vendeur des certificats de conformité. Parmi les fabricants, de confiance par les experts, il existe plusieurs marques.
"Borovichi"
Sous cette marque, vous pouvez trouver un mélange de maçonnerie réfractaire pour le four, ainsi que la solution pour les cheminées. Des bouchons professionnels introduisent souvent dans ces compositions une pâte d'argile, une argile diluée à un état semi-liquide, ce qui améliore l'adhérence du mélange.
ScanEx
Société nationale produisant des mélanges pour briques en céramique sous la marque TERM SA, chamotte - TERM TK.Ces derniers sont de la maçonnerie, car ils ont une propriété réfractaire due à la composition argile-silicate. L'option pour les briques en céramique est le ciment-sable, elle ne convient donc que pour l'exécution des murs extérieurs des structures. Enfin, le même fabricant propose un mélange TERM AL, qui est un enduit pour les murs extérieurs.
"Plitonite"
Le produit est une production germano-russe. Vendu en plusieurs versions.
Parmi les produits les plus populaires, notons les compositions suivantes:
- "Pose Thermique". Ce sont des produits utilisés pour les murs extérieurs de poêles, cheminées. Diffère en efficacité matérielle.
- "Réfractaire". Le matériau est destiné aux briques résistantes à la chaleur.
- "Thermoglue". Composition adhésive pour le revêtement du four, par exemple des carreaux de céramique.
"Vetonit"
Les produits de cette marque sont disponibles en trois versions: pour les cheminées - la série SVL; pour les chambres de combustion, ainsi que pour les surfaces en contact avec le feu ouvert, des composés appropriés TM; la composition des éléments exposés à des températures ultra-élevées (1200-1300 degrés) permet la composition du téléviseur.
"Terre cuite"
Un autre fabricant russe qui a reçu de nombreuses critiques positives.Il produit des mélanges à base de chamotte et d'argile kaolin, de sorte que le produit fini puisse résister à une chaleur allant jusqu'à 1 300 degrés. Diffère la plasticité, ce qui facilite l'utilisation.
RATH
Société autrichienne spécialisée dans la production de mélanges pour fours réfractaires résistant à la chaleur. Le prix élevé, selon les acheteurs, est justifié par des produits de haute qualité, une facilité d'application (permet de mettre des coutures fines) et un séchage rapide.
Maison de four "Makarov". C'est l'un des principaux fabricants russes, dont les produits sont bien connus en dehors du pays. Les mélanges de cette marque sont largement utilisés par les bouchons professionnels, ce qui témoigne de leur grande qualité. Dans le même temps, en raison de la facilité de reproduction et de l'élasticité, ils peuvent être utilisés par des personnes ne possédant pas de compétences professionnelles en construction. La base de la composition - variétés d’argile cambrienne bleue et rouge.
Comment le faire vous-même?
Lors du mélange de la solution pour le four, il convient de rappeler que chaque partie requiert une composition spéciale. Par exemple, la partie souterraine peut être réalisée avec du mortier de ciment conventionnel.Cependant, les surfaces en contact avec une flamme nue et exposées à la chaleur doivent contenir de l'argile. Le mélange pour la base est malaxé à partir de ciment et de sable, dans un rapport de 1: 3. Il est également acceptable d'ajouter de la pierre fine broyée à la solution. Il devrait être dilué avec de l'eau jusqu'à une consistance semblable à celle d'un sol humide. Le sable pour la composition vaut mieux prendre la montagne. Rugueux, ces grains de sable offrent une adhérence plus élevée contrairement au sable de rivière poli par les vagues.
Le mortier prend en une demi-heure, la solidification complète a lieu dans la journée, après quoi il est possible d'effectuer la pose.
La maçonnerie est réalisée à l'aide d'argile de chamotte brûlée, versée avec de l'eau et pétrie jusqu'à obtenir la consistance d'une crème sure épaisse. Il est possible d'augmenter la résistance des joints de maçonnerie en ajoutant du ciment au mortier et d'accélérer le séchage en ajoutant de la chaux. Lors de l'ajout de ciment, 2 parties d'argile, 1 partie de sable et un tiers de ciment sont prises. Le ciment ne doit pas dépasser 10% du mélange total. La Chamotte est une argile réfractaire à haute teneur en alumine, précuite, qui comprend également des composés de la grenade minérale et de la chicorée.En vente chamotte peut être trouvé sous le nom "Mortier". Il est important que l'argile ait une teneur moyenne en graisse. Cet indicateur peut être déterminé comme suit: une balle ou une saucisse doit être roulée en argile, après quoi elle doit être comprimée ou étirée. Si des fissures apparaissent à la surface, cela signifie qu'il y a beaucoup de sable - la teneur en matière grasse de ces matières premières est faible et ne convient pas pour l'ajout au mélange.
Vous pouvez également placer la balle roulée entre deux petites planches qui doivent être comprimées lentement. L'optimum est une composition dans laquelle les fissures sur la balle n'apparaissent qu'après compression par une troisième. Si ces phénomènes se manifestent plus tôt, la teneur en graisse de l'argile ne suffit pas. Si la fissuration n'est pas observée pendant une période trop longue, l'argile est trop liquide. Dans le cas de l'utilisation de matières premières maigres ou trop grasses, les coutures se fissurent et s'atténuent de manière inégale, de sorte qu'elles ne conviennent pas. Dans certains cas, des matières premières trop grasses peuvent être corrigées en ajoutant du sable.
L'argile a besoin de bien tamiser, en éliminant les impuretés. Pour le nettoyage, vous pouvez utiliser la méthode du poêle expérimenté - l’argile est coulée dans la partie supérieure de la surface inclinée avec une couche uniforme ne dépassant pas 30 cm.Versez de l’eau de telle sorte qu’elle n’atteigne pas l’argile. Ensuite, avec une truelle ou des mains, des vagues sont créées qui lavent l'argile. Après un certain temps, la matière première reste dans le liquide, qui est ensuite séparé de l'eau et filtré à travers un tamis. La prochaine étape consiste à tremper la matière première obtenue dans de l'eau propre pendant 24 heures. Après le temps spécifié, la composition est à nouveau agitée, si nécessaire, versez de l'eau.
Après cela, vous devez prendre des bidons de cinq litres, dont deux sont complètement remplis d'argile purifiée. Le troisième pot n'a besoin que d'un tiers pour se remplir d'argile, le reste de sable. Le pot suivant doit contenir encore moins d'argile - la quatrième partie, et les parties restantes sont également recouvertes de sable. La dernière banque ne devrait contenir que du sable.
L'étape suivante consiste à mélanger les ingrédients secs de toutes les boîtes et à les verser avec de l'eau. Pétrir la composition des mains plus commodes. La consistance de celui-ci devrait ressembler à la crème sure et ne pas coller aux mains. Les artisans professionnels vérifient généralement la résistance de la composition en faisant rouler une boule d’environ 5 mm de diamètre. Ensuite, la balle est complètement séchée (environ 10 jours), après quoi elle tombe d’une hauteur de 1 m.Si la balle ne s'effrite pas et ne se déforme pas, la composition est considérée comme durable et de haute qualité.
S'il n'y a pas assez de temps pour attendre que la boule d'argile se dessèche, vous pouvez fixer deux briques avec la solution préparée. Après cela, attendez 5 minutes et soulevez les briques par la partie supérieure - la brique inférieure ne doit pas tomber ou «ramper». Le mélange de haute qualité résiste à plusieurs de ces altitudes.
Le four est généralement enduit d'un mélange à base de chaux et d'eau. Du gypse ou du ciment est également ajouté pour augmenter les caractéristiques de résistance de la couche. La chaux est pré-tamisée, brisant les morceaux. Ensuite, tous les ingrédients secs sont bien mélangés et remplis d’eau tiède. La solution obtenue, dans sa consistance, devrait ressembler à de la crème sure épaisse. Lorsqu'il est supposé que les surfaces en plâtre sont fortement chauffées ou que la composition de revêtement est utilisée depuis l'intérieur du four, une colle à base de silicium y est ajoutée, ce qui procure une résistance à la chaleur. Cet additif est généralement acheté dans un magasin spécialisé - il est mieux connu sous le nom de verre liquide. Dans la solution finie, son contenu doit être inférieur à 20%.
La recette avec du verre liquide peut ressembler à ceci: 3 parties d’argile et de sable sont combinées à 1 partie de verre liquide et la même quantité de poudre de dentifrice.
La recette de plâtre traditionnelle comprend 1 partie de chaux, 2 parties de sable et un dixième d’amiante. Vous pouvez obtenir une composition plus durable, en prenant la même quantité de sable et de ciment (ensemble, ils forment une partie), ajouter 2 parties de sable et un dixième d'amiante. Si nécessaire, en face du four avec des tuiles, on prépare la composition suivante: 1 partie de mélange argile-ciment (se compose de quantités égales d'argile et de ciment), 2 parties de sable. Parfois, du sel de table est ajouté, ce qui augmente les propriétés de résistance et empêche la fissuration des coutures.
Certains maîtres refusent d'ajouter de l'argile à la solution en mélangeant la composition de ciment, de sel et de sable. Les ingrédients sont pris en quantités égales. Cependant, pour ce mélange, les carreaux doivent être trempés dans l’eau environ 2 heures à l’avance. Renforcer l'adhérence et empêcher de coller sur les carreaux permet l'approfondissement des joints de maçonnerie.
Instructions d'utilisation
Les solutions préparées doivent être versées avec le volume d'eau spécifié par le fabricant et mélangées avec un mélangeur ou utiliser une buse sur une perceuse. Le mélange avec des outils est nécessaire car il est difficile de le faire manuellement, ce qui oblige à ajouter plus d'eau à la composition. Ceci, à son tour, contribue à la modification des caractéristiques du mélange.La quantité de préparation du mélange doit correspondre à la quantité de travail pouvant être achevée en une heure. Il est donc préférable de le préparer par petites portions. Il est inacceptable d'ajouter de l'eau ou d'autres solutions au mélange congelé pour le pétrir à nouveau.
Les ingrédients secs sont versés dans de l’eau tiède, bien mélangés, puis la composition doit être laissée au repos pendant une heure. La consistance doit obtenir un mélange ressemblant à de la crème épaisse. Si ça casse, vous devriez ajouter de l'eau. Si, lors du ratissage d'un composé à la truelle, il en reste une trace à la surface, il y a trop de liquide. Lorsque vous ratissez la solution avec une truelle sur le côté, elle doit conserver sa forme et ne pas se déchirer.
Lors de l'utilisation de solutions prêtes à l'emploi, il est également possible de ne pas tremper les briques, car les mélanges secs sont caractérisés par leur capacité de rétention d'eau, ce qui permet de raccourcir la durée d'installation du four et de sécher la maçonnerie.
La solution est appliquée avec une truelle de 10-12 mm d'épaisseur. Les mélanges secs vous permettent de former une couture mince (de 2 à 4 mm), ce qui vous permet d'éviter de la fendre, de conserver la composition et d'obtenir un résultat plus attrayant.Le travail devrait être à une température de +10 à +35 degrés Celsius. Conservez la composition doit être non diluée, dans un emballage d'origine scellé, dans un endroit sec et chaud.
Conseils utiles des pros
Bien que les fabricants de mélanges prêts à l'emploi indiquent la quantité d'eau requise, son volume dépend de la température de la pièce. Un peu plus d'eau est requise à des températures élevées dans la pièce, et un peu moins à des températures basses (dans les limites de la normale, mais non inférieures à +10 degrés). Des cuisiniers expérimentés ajoutent parfois du sel au mélange de réfractaires, ce qui permet d'augmenter la résistance du joint. On prend 150 grammes de sel pour 10 kg de composition sèche. Au lieu de sel, 1 kg de ciment peut être ajouté au même volume de solution - la qualité M400 sera suffisante.
Il est recommandé de choisir différentes compositions pour la cheminée, en raison de la différence de conception et de fonctionnement. Les éléments de la cheminée chauffent moins (en fait, seule la partie du four est exposée à des températures élevées), de sorte que la résistance accrue à la chaleur n'est pas nécessaire ici, mais la résistance et la résistance à l'humidité sont importantes. À cet égard, pour les foyers, les experts recommandent de diluer le mortier de chaux-ciment et, pour le four, une composition argile-chamotte.
Après 3-4 jours après la cuisson au four avec des mélanges secs, vous pouvez commencer à chauffer l'appareil. Cela devrait être fait activement pendant encore 3-4 semaines, après quoi vous pouvez produire une doublure. Si, après un essai de chauffage du four, des efflorescences se sont formées dans la zone des joints (ce qui est considéré comme normal), elles peuvent être éliminées avec un chiffon humide après le refroidissement du four.
Pour apprendre à préparer un mélange pour la pose de briques, voir la vidéo suivante.