Which floor screed solution is better?
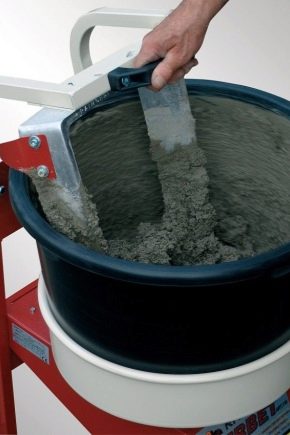
When buying a new home, everyone wants to see perfectly flat surfaces on the floor and walls of the room. But reality often does not coincide with desires. The irregularities of the walls or floors are usually immediately apparent and correcting the mistakes of past owners is the main goal of the new settlers. And, most importantly, properly align the floor.
Twenty or thirty years ago, builders leveled floors only with cement. Now there is a huge amount of various additives and impurities., technologies go ahead and change, in accordance with the requirements of consumers. Also increases the strength of the screed, and simplifies the process of pouring the solution. On the features of solutions for screed will discuss in our article.
What it is?
To understand what a floor screed solution is, it is necessary not to make mistakes in any of the stages of work or preparation for it.
There is a certain range of tasks that are solved with the help of flooring:
- Make the floor surface completely flat.
- Strengthen the coverage.
- Improve thermal insulation.
- Improve sound insulation.
- Increase the height of the floor.
- Preparation before laying and installation of systems of a heat-insulated water floor.
- Evenly distribute the load.
- If necessary, create the necessary slope of the floor space.
Screed - a layer of concrete between the main and decorative floor coverings.
Features and types of mixtures
Modern technologies allow us to achieve excellent results using different types of floor screed compounds:
- Concrete. The most durable, used when necessary to make a solid foundation. They will suit both residential and industrial premises. The composition includes cement, sand, gravel and gravel. When using such floors, it is necessary to correctly observe the proportions so that the parameters you specify are preserved.
- Cement. Pretty universal type of mixture. Waterproof, which allows you to work with it and use in any rooms with high humidity: kitchens, bathrooms, garages. The main disadvantages include the fact that this screed cracks when using a very thin layer,therefore, the layer must be larger, or this work will need to be entrusted to a professional.
It is also necessary to remember that such mixtures shrink more during drying. Often, when using this type of mixture, a metal reinforcement bundle is also installed.
- Anhydrite. They are also called plaster. They have high strength, it allows stacking with a thin layer. Do not change their properties when temperature drops. They are very easy to use, so they are often used by those who are not very strong in construction.
Anhydrite is very plastic, therefore it is easy to level. Dry up such floors for two days.
This type of screed is not subject to shrinkage in the process of drying, so you will know exactly the thickness of the floor in the end. The main disadvantage of this screed - can not be used in rooms with high humidity.
Also on the market you can see the finished mixture, in which all proportions have already been observed. You only need to choose the solution, the properties of which you will need. The presence of such mixtures facilitates the process of mixing, makes styling easier, also increasing the fluidity of the resulting solution.
The composition of the finished mixtures is chosen so that they are easier to align with the floor surface, the shrinkage is minimal. It is worth noting that the price of such ready-made mixtures is much higher than that prepared by themselves. Therefore, it is necessary to decide whether you will use the ready-made mixture or buy all the elements separately, and will make the solution yourself.
Cooking recommendations
For self-production of cement mortar you will need:
- Sand. It is necessary to sift from the large sand fractions, stones, rubble. It is also necessary to sift the sand from the garbage.
- Cement. For screed floors in residential areas is best to use cement M-400. It must be remembered that the brand of cement decreases with time, and its properties do not change for the better. Always use fresh cement.
- Water.
- If necessary or desired, special additives and impurities to obtain the properties you specified.
You also need to know how to properly stir the solution:
- In the tank, where the elements will be mixed, you need to fill the cement and sand. It is necessary to observe the correct proportions, most often 3 kg of sand should be used for 1 kg of cement.
- In another tank, water and plasticizer will be mixed.It is necessary to use them at the rate of 200 g of impurities per bag of cement. The calculation of the amount of polymer fibers and other additives is made according to the instructions indicated on the package with the additive.
- In the dry mixture, it is necessary to make a depression in the form of a trough in the center in order to calmly and gradually add water. The consistency of the resulting solution should resemble thick sour cream. The mixture should be easy to get off the trowel.
It must be remembered that the volume of the prepared mixture must correspond to the time for which it can be fully developed. Most often - it is one and a half or two hours. Consumption for a certain time is difficult to calculate, it depends on the speed of work and on the number of people. After two or three hours, the solution hardens, hardens, and its properties deteriorate.
Most often for mixing the mortar used concrete mixer: manual or electric. This allows you to significantly speed up the process. Also often mixtures are made in old baths or large troughs. A sapka or shovel is used for mixing the ingredients - it all depends on the volume of the solution and on the person’s physical fitness.
In the manufacture of a small amount of the mixture in the bucket you will need to use a drill with a nozzle. Such nozzles can be found in any hardware store, because it is very convenient to interfere with them.
Fill rules:
- First you need to make the priming of the subfloor. This will improve the adhesion of the old coating with the new solution. If the rough floor is porous, then it must be treated with a primer (a viscous composition for primer).
- Before filling, special beacons are almost always installed. They allow you to monitor the evenness of future floors in the process of pouring mortar. Without them, you can achieve a flat surface, but the process will take much more time.
- In the installation of lighthouses there are no special difficulties. Knead the plaster solution and make the tubercles to a height not exceeding the height of future floors. On these bumps fit either slats made of wood or thin metal profiles. They are installed at a distance not exceeding the length of the rule.
With the help of the rule and level we align beacons in one plane, while creating an absolutely flat surface. The pouring process itself can be started when the gypsum dries completely to avoid beacon shifts.
- The process of pouring is done in strips in order to constantly monitor the evenness of the area where the mixture already exists. Installed beacons serve as a formwork. The surface must be flattened by the rule. The supply of the solution can be done with a trowel or spade, depending on the room and the amount of work.
- The formation of bright spots on the solution means that there are depressions and bumps. To eliminate cavities, it is necessary to add a certain amount of the mixture to that place, and level the whole plane again by the rule. The tabs are also equal to the rule.
- It should be borne in mind that drying can occur unevenly throughout the depth of the layer. As a result, cracks may form. To avoid this, the entire surface of the screed cover a special polymer composition. The main thing is to do it evenly and on time. It is necessary to apply this layer in 7-8 hours after filling the floor with the basic solution.
Professional Tips
Often before a choice of material there is a question, what is better - a mixture of cement and sand or concrete?
Most often, professionals prefer concrete:
- If you use concrete together with expanded clay, you can get floors with excellent thermal insulation.
- When using concrete with rubble, you get a floor that can withstand enormous loads.
- Concrete can be poured directly on the ground.
- With concrete, you can get a completely monolithic base.
- It is easier to lay decorative coating on concrete.
It is also necessary to remember about the requirements of SNiP. The floor must withstand 150 kg per square meter of surface. The strength of concrete or other type of screed should be 15 MPa. Compliance with these standards guarantees a long service life.
Masters advise to slightly moisten the composition in the process of floor screed. This prevents the surface from cracking. Often masters advise beginners to rent or buy a mortar pump in order to use the solution evenly and quickly. This unit is used for any kind of mortar mixes.
In conclusion, we can say that there is no definite recipe for mortar under the screed. There are correlations that are used most often, but for each case it is best to calculate everything yourself. Knead and properly lay the solution, as well as choose the correct ratio of components in the mixture mix - this is the key to successful work.
To learn how to prepare a solution for floor screed, see the following video.