Features and methods of mechanized floor screed
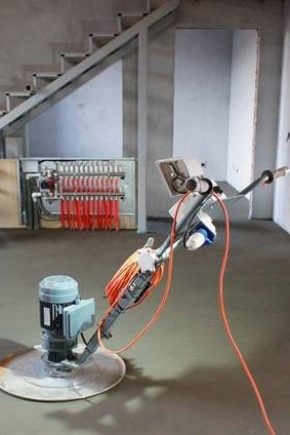
Mechanized or semi-dry floor screed - one of the fastest and high-quality technologies for pouring the floor today. Good results are achieved thanks to experienced professionals and the use of modern equipment. But with careful execution of the algorithm of actions, taking into account the characteristics of the mixture and the correct application of this method, you can get a perfectly flat floor yourself.
Finishing the floor - an integral part of the repair work. The most popular materials for this are linoleum, laminate and parquet. So that these materials are not wasted, it is better to worry about the foundation of the floor in advance, namely about its screed.A screed is a transition layer between the slabs and the floor covering. It is on the quality of the screed depends on the durability of the floor covering.
Kinds
Screeds come in different forms:
- wet
- dry;
- semi-dry (mechanized).
The very first technology of pouring floors was a wet screed. She owns almost any builder. As the name implies, a flowing cement concrete solution is created, which is subsequently poured onto the surface. After pouring, a lot of additional processing work is carried out, as there is a huge risk of cracking due to the high moisture content. The use of large amounts of water in this method is the reason for the long drying of the screed.
In practice, dry screed is often used, which must be done by an experienced specialist. The bottom line is the use of dry bulk filler - expanded clay (expanded clay sand) and laying gypsum-fiber sheets.
Unlike a wet screed, dry does not require a large amount of time to mature and is actively used in winter. If improperly performed, the floor can be very curved and cannot withstand heavy loads.Also, the screed may begin to crumble and break off.
Today, many people prefer a semi-dry screed, which is carried out in a mechanized way. Special machines are an essential attribute for the competent implementation of the technology of forming a semi-dry machine tie. Mechanical coupler has many advantages.
Features: pros and cons
Mechanized floor screed has the following advantages:
- Accelerated curing, which is achieved by using less water. Moisture evaporates much faster than other methods.
- Reducing the number of cracks caused by shrinkage of the floor. The effect is caused by the fact that the water contained in the pores of the skeleton of the screed is there in small quantities, and the evaporation process does not cause significant formation of cracks, cavities and voids both on the surface and inside the screed. You can also use reinforcement with a special fiber to impart a mixture of strength and improve the bonds between its particles.
- No problems with the solution. Due to the fact that the equipment supplying the mixture, is located outdoors, the problems associated with contamination during cooking, disappear.There are no problems of leakage of the composition in the space between the plates due to the low moisture content in the mixture.
- Does not require additional alignment. In other words, the floor becomes perfectly flat, and for the final stage only disc trowels are needed. It is also a major advantage in mechanized plastering of walls.
- Reducing the influence of the human factor.
The process of mechanized screed is almost completely automated. Therefore, the risk of cracking, getting uneven laying and floor curvature is minimized.
The disadvantages of this method include:
- Large financial costs when using equipment. These expenses are due to the fact that expensive tools and devices are used for the screed, which significantly increases the cost of the work, as they require the presence of specialists. It is much more profitable to buy equipment for companies that want to provide services of this type. For those who want to make a disposable tie, it will not always be profitable, even when renting appliances.
- Large areas. Companies usually do not take up small areas up to 100 m2.If you need company services for small areas, it is desirable to find people who also need a floor screed in the apartment. The best option may be neighbors, with whom you can make one general order for several apartments.
- High screed. With the semidry method it is almost impossible to achieve low screed heights. The minimum possible height of the screed is 4 mm.
- The difficulty of selecting the optimal ratio of components of the solution. There is no specific rule for cooking the mixture. Recommendations for ratios are indicative. Preparation of the mixture without an experienced master often does not bring the required results, since for each case an individual approach is required.
Technology
For high-quality work on the semi-dry technology requires special equipment:
- Pneumosupercharger. Pneumosupercharger is used to prepare, knead and feed the mixture to the place of installation. The equipment allows you to hold the screed in high-rise buildings, without lifting the components of the mixture for cooking in the room.
- Grinding (zatirochny) machine. Grinder is used to level the floor.It seals the screed and removes minor irregularities. After work, the trowel can immediately put even the most sensitive laminate and parquet.
- Concrete vibrator. A vibrator for concrete is used for tighter laying of the screed mixture. The principle of operation of the device lies in the electric motor, which forms oscillations of a given frequency. Oscillations are transmitted to the components of the screed, due to the vibration of the particles re-compacted and form a more stable mixture.
How to make fill your own hands?
The technology of pouring a semi-dry screed with proper carrying it out can be done with your own hands without special equipment.
The general algorithm includes the following steps:
- surface cleaning;
- calculation of the amount of solution;
- preparation for waterproofing;
- laying a layer of waterproofing;
- laying beacons;
- preparation of the mixture;
- filling the mixture;
- tamping, comparing and grinding the surface;
- maturation screed.
Surface cleaning
Before work, the surface should be prepared by removing all the accumulated debris. It is necessary to vacuum the cement dust and seal up the slots of the plates.If you are replacing and updating the previous tie, you must first get rid of it completely. It is better to remove the old layer of the screed, even if it seems that it is well preserved.
Calculate the amount of solution
In order to calculate the right amount of solution, you must first carry out work on the measurement. First, the level of the horizon on the walls is determined. For this purpose, one mark is placed on any wall with which the horizon is drawn along the entire perimeter of the room. The highest point is determined to check the height difference of the floor and base by the method of horizontal transfer of the label using levels.
After that, the amount of the required solution is adjusted, taking into account that for each bias in 1 mm with an area of 100 m2 it takes about 0.16 m3.
Preparation for waterproofing
Before the waterproofing can be carried out with a ground solution, which will increase the waterproofing and strengthen the surface of the base. You can also glue the damper tape to provide additional waterproofing and protect the concrete from cracking.
Laying a layer of waterproofing
There are 2 methods of waterproofing: coating and roll.Polyethylene film can be used as a manual roll waterproofing. The strips of the film are overlapped with a permissible overlap of 10 cm. It is not necessary to fix the film, but for convenience, you can fix the edge on one side to the wall.
Laying lighthouses
T-profile slats (this profile is best suited for a semi-dry screed) with a large step for leveling the surface are called beacons. They are placed parallel to one of the walls. Beacons are usually set at a distance of 10 cm less than the length of the rule. However, the location of the first beacon is measured from the selected wall at a distance of 30 cm.
Mix preparation
Components of the mixture:
- cement;
- sand;
- fiberglass;
- plasticizer;
- water.
Cement is a link between the particles of sand, it is necessary to choose it depending on the requirements of the floor.
There are different brands of cement for screed:
- M 400-T and M 400-D20 (the ratio of cement and sand for this brand is 1: 3);
- M 500-T (the ratio of cement and sand for this brand is 1: 4).
Cements below 300 are usually not used for screeding, as they do not withstand the load required for the floor.Cement brand M 400-T is cheaper than M 500-T, but it is required more. Also a good choice can be M 400-D20, which has in its composition a plasticizer.
The sand must be washed and sifted. It is advisable to choose coarse sand, because it forms a more durable substance when mixed with cement.
Fiber is an additive that is used to reinforce the mixture. It is an elongated filamentous shavings of small thickness. Used to prevent the formation of cracks and increase the life of the screed.
There are two types:
- basalt fiber;
- polypropylene fiber.
Basalt fiber is more expensive and is used in specific cases. For example, it is used in areas of frequent earthquakes and in conditions of high humidity. Polypropylene fiber is the most common and inexpensive counterpart. There is a risk to purchase low-quality goods. It is best to buy supplement in proven hardware stores, and not from private sellers.
Plasticizer is a chemical additive, which serves to impart different properties of the mixture depending on the type.The plasticizer is used to impart strength and uniformity. Also at its application frost resistance properties increase. It can significantly reduce the drying time of the screed, but an additive is selected depending on the requirements.
The ratio of cement and sand is selected depending on the brand of cement. The amount of water is determined by eye. The consistency after mixing should be homogeneous, loose and not fluid.
Filling mixture
Fall asleep the resulting mixture, starting from the opposite end of the door. Usually two people pour the mixture at the beacons. The best way to work is when one person lays the mixture, and the second at this time levels it.
Tamping, comparing and grinding the surface
Tamper mixture should vibrokladchikom, but you can walk on the surface of the rule. Grind the surface with a trowel, but with manual grinding you can do with a wide grout, which must be rubbed in a circular motion, applying pressure.
Maturation screed
The tie can be covered with film for best results. Approximately 15 hours later, waiting for the screed to close. After you are allowed to walk on the surface.And only after 3 days you can do the final finishing of the floor.
Reviews
Most people, as practice shows, have heard about the technology of semi-dry screed and find it most effective for the repair work of the floor in the apartment. Also, users note the quick turnaround time, they are satisfied with the drying time.
When contacting a company, people advise:
- Consciously approach the choice of company. It is advisable to ask your friends and read reviews about the company on the Internet. If there is little information about the company, you should ask about the ratio of components in the solution when pouring. Often there have been cases when unscrupulous specialists of companies tamped clean sand with water.
- Discuss the order conditions in advance. It is worth asking if cleaning services are included in the list of services. Although the technology of mechanized screed is the most clean, but, nevertheless, construction debris in the form of cement sand and mixtures can remain in the stairwell and in the yard. This can bring additional trouble, for example, for residents of high-rise buildings.
Interesting work options
In this video you will find a master class on laying a semi-dry mechanized floor screed.