Fiber for floor screed: features of use
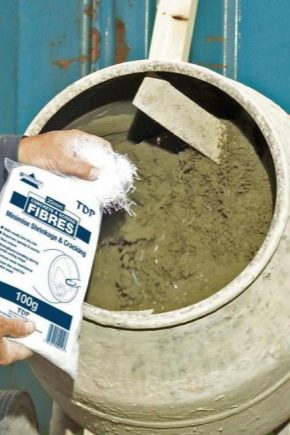
Reliable, even and warm floor is not only the dream of everyone about comfort and coziness, but also strict requirements of building rules and regulations. Modern technologies make it possible to realize such a dream and get a quality result without flaws. The right and durable floor today can even be assembled by a non-professional. One of the important stages of work on the arrangement of the floor is to fill the screed.
Specifications
According to technology, the tie must be reinforced. Concrete, in addition to its strength, has brittleness, which must be compensated. For different types of screeds, there are different types of reinforcing materials and methods. They can be used separately, and can be used in combination. One of the most advanced materials is fiber.
Fiber elements are made of metal, basalt, polypropylene and fiberglass. Fiber is used not only for the reinforcement of screeds. It is also added to the plaster, mixed in a mixture for pavement, used in pouring the foundation, piles. Fibers are distributed evenly throughout the entire volume of the solution, and create multidirectional reinforcement. Formed a single structure.
Due to this, the characteristics of the concrete layer are significantly improved:
- Decreases time of hardening of the mixture
- Strength increased by 90%.
- It becomes longer service life.
- Increased resistance to mechanical stress.
- Reduced moisture absorption.
- Plasticity of concrete, its viscosity, ability to suppress fluctuations improves. This allows the use of fiber reinforcement in the military and heavy industries.
- Resistance to temperature fluctuations, frost resistance.
- Increases resistance to abrasion. It is important for use in dams, reservoirs, dams.
- Reduces the risk of cracks and delamination.
Fiber elements of all kinds are compatible with all additives and components of the mixtures for casting.
Species
Metallic fiber is made in different ways. It is made of stainless steel sheets. The length of the steel elements is 20-50 mm. The pieces of wire of different shapes are covered on top with a layer of brass. They are usually wave, in the form of anchor and corrugated elements. The wire is made from low carbon steel, length - 50-60 mm, diameter - 1 mm. Steel fiber is used:
- in the industrial and loaded floors;
- hanging panels;
- stilts;
- basements;
- shopping centers and high traffic areas.
In addition, this material is used when pouring foundations, prefabricated structures, monolithic street and supporting concrete structures. At its ends are special bends, which contributes to a more reliable adhesion with the layer of screed. Basalt fiber perfectly withstands shock loads. This material is effectively used for floors that are planned to increase the load. The main advantages are:
- Fire safety of the material, environmental cleanliness, neutrality to various chemical environments.
- When interfering with the solution, the fibers fully adhere to it.
- Basalt fiber is used for the construction of heat-resistant concrete structures.
On 1 square. m of concrete consumed from 1.5 kg of fibers, the consumption of cement and water decreases when using basalt fiber by 15-20%. Polypropylene fiber is made of synthetic material. Fibers are soft and flexible, light, white, 18 mm long, diameter is 20 microns. Polypropylene fiber does not conduct electricity. For better adhesion to the structure of the solution, it is impregnated with a special oil substance.
Fiberglass fiber is very resilient and elastic, therefore it is recommended for finishing facades of buildings, concrete products of complex shape, as well as products for decoration and decoration, garden sculptures, arches. This material reduces water consumption in the preparation of the mixture by 20%.
Advantages and disadvantages
This remarkable material has no obvious flaws. For the price, fiber reinforcement is quite affordable. Poor quality fake during operation will produce toxic substances that harm the welfare of the owners. At all stages of the formation of the floor fiber reinforcement helps to prevent deformation, protects the screed from cracks. Immediately after pouring, the fibers retain the shape of the screed, and are evenly distributed throughout the volume.
At shrinkage of the drying concrete reinforcement maintains loading. During strength and final drying, the fiber reduces stress in the cement layer.
Using fiber, it is possible to reduce the absorption of moisture in the screed by reducing micropores and microcracks, to improve the adhesion of the solution to the base, thereby facilitating the alignment and speeding up the drying. The frost resistance of fiber reinforced concrete makes it possible to successfully use it in the northern regions. Steel fiber elements are the most durable, at the same time, they have considerable weight.
Of course, under very high loads or harsh operating conditions, reinforcement only with fiberglass, even steel, may not be enough. To solve such problems, complex fiber reinforcement and reinforcing mesh are used.
Mixes of the best quality and desired properties are obtained if all the ingredients are properly and thoroughly mixed. It is necessary to mix the fiber elements with the dry components of the future solution, gradually adding them to distribute the fibers without forming lumps, then add water and a plasticizer.
How to choose?
With such a variety of reinforcing additives, the problem of choosing the right material for each particular case arises. The choice depends on several factors: type of construction, area of the room, its purpose, on what thickness of fiber floor screed, operating conditions, planned loads. It is important that the fiber was purchased in a safe place, there were all the accompanying documents, certificates of conformity, instructions, so that it was manufactured at the factory:
- For "warm floors" in apartments and standard home leveling coating, the most rational is the use of polypropylene fiber. It is a lightweight material that does not increase the overall weight of the screed, does not conduct electricity, and does not create electromagnetic fields.
- For monolithic reinforced concrete structures with heavy equipment on the floor, heavy loads and mechanical stress, steel anchor fiber is the best solution.
- Fiber glass is recommended for garden sculptures and arches, fences and facades. Its elastic structure allows you to create objects of complex shape.
The length of the elements also affects the choice of scope of use:
- for brickwork and exterior cladding, the fiber length should be at least 6 mm.
- For monolithic structures, the fiber length must be at least 12 mm.
- For dams, complex buildings and structures, as well as under aggressive conditions, a length of 18 mm is important.
- For semi-dry screeds and repair activities suitable fiber in 18 mm.
All types of fibrovolokon receive excellent feedback from specialists who use these materials in various areas of construction and in different regions of our country.
Thanks to such fibers, it has become possible to build in earthquake-prone regions, and in the north, where in winter extremely low temperatures. Excellent feedback comes from the owners of the apartments, who made a quick and inexpensive repair using fiber. They note the excellent result and durability of the floor, affordable price and reduced repair time.
How much to add?
With a different amount of fiber fibers added, a solution with different technical characteristics is obtained. Calculation of the solution consumption is per 1 m2. Cement and sand are mixed in a ratio of 1: 3, then reinforcing materials are added to the resulting dry mixture, and then water is added to obtain a semi-dry consistency of the mixture.The calculation of the dry material consumption is in grams per 1 m3 of solution. Of course, the greater the weight of the additive, the stronger the coupler will turn out, but there are certain norms:
- If the proportion of fiber is 300 g, then the concrete is easier to lay down, it becomes more plastic, fills the gap.
- If you add 500-600 g, the strength parameters of the finished layer will increase significantly, and no shrinkage cracks will occur upon drying.
- With the addition of 800-900 g, the concrete gains its maximum strength and acquires all the properties of the reinforced layer.
- Fiberglass fiber is consumed in the amount of 1 kg per 1 m2.
- Popular polypropylene fiber is sold in bags of 10 kg. There is a packing of 18 kg each: in a bag - 20 bags of 900 g each or 30 bags of 600 g each. Such packing is convenient for preparing a solution.
It is not necessary to weigh a portion of the fibers with each batch. The price for 1 kg of fiber, on average, is 250 rubles.
Technology use
All stages of creating fiber-reinforced coatings are so worked out and verified that getting the right result without defects is available even without recourse to professionals, while working independently. To fill reinforced screed, you must have the following tools and materials:
- cement, sand, water, plasticizer, fiber;
- damping tape;
- level: laser or ordinary water;
- profile for lighthouses;
- rule, tape measure, ruler;
- drill with nozzle for mixing solution;
- roller for leveling semi-dry screed (if necessary);
- screwdriver, fixing materials (screws);
- construction knife, trowel and trowel.
The stages of work are as follows:
- First you need to prepare the base for the base tie. To do this, remove all debris, dirt and dust, and carry out wet cleaning. The surface should be dry and clean. Next, you need to seal all the cracks and irregularities with putty, walk along the base with a primer for the best adhesion.
- Find the highest point of the future screed, mark with a level on all walls.
- Install beacons that will align the surface of the screed. Lighthouses are made from a profile. They are fixed at the required height with plaster mortar or cement. After alignment, the beacons will become flush with the surface.
- A special damping tape is glued around the entire perimeter of the room at the bottom of the walls and around the columns and podiums for plumbing, which performs a compensating function when concrete is expanded as a result of temperature drops, for example,with the inclusion of "warm floor". Along with the fiber, it prevents the deformation and cracking of the screed during drying.
- Insulating materials are laid, if necessary, reinforcing mesh, heat insulation and a “warm floor” heating circuit are installed.
- Preparing a solution. One part of the volume of cement is taken 3 parts of the volume of pure sand, from 300 to 900 g of fiberglass. All ingredients are mixed, then water and plasticizer are added to the dry base mix. If the solution is mixed thoroughly, a high-quality fiber cement screed will be obtained.
- The finished reinforced solution is applied to the prepared surface with a thin layer of 3-5 cm. It is necessary to take into account that the semi-dry screed "shrinks" 1 cm after tamping.
- The coupler is leveled by sliding along the guide beacons, or a semi-dry coupler is rolled with a special roller.
- Waiting for drying and curing. To do this, the finished screed cover with plastic wrap, moistened once a day with water. The time to build strength is 1 week. Full cure time is 2-3 weeks.
Reinforced reinforcement screed ready. You can start laying the finishing decorative coating.
You will learn more information about fiberglass for floor screed in the following video.